Aerospace Projects
Metallic/composite airframe and spacecraft structural design for manufacturing, tooling and assembly engineering support

- metallic/composite/ LO structures

-thermoset vs. thermoplastic component builds

- looking inboard at forward fuselage air frame assembly

-Looking forward at aft bulkhead

-co-consolidation curing with dissolving mandrels

-Cypac / PEEK based laminate assemblies co-consolidated / co-cured
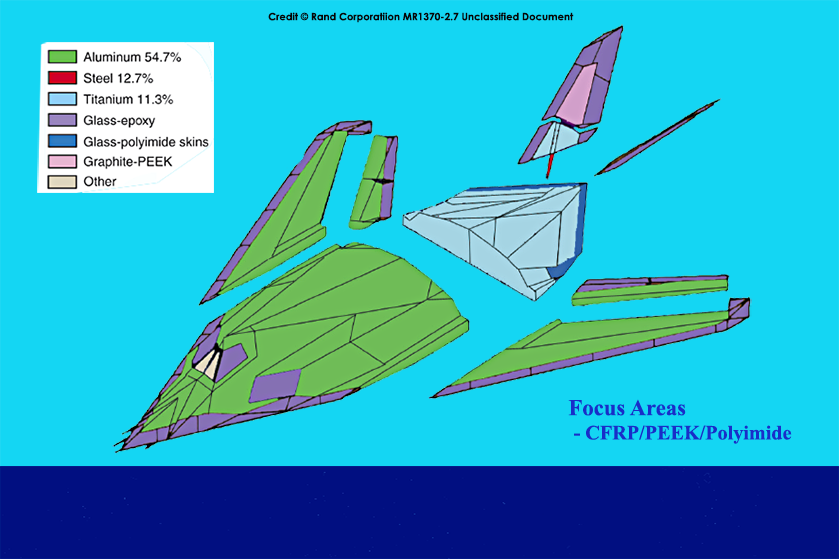
-out of autoclave cure development
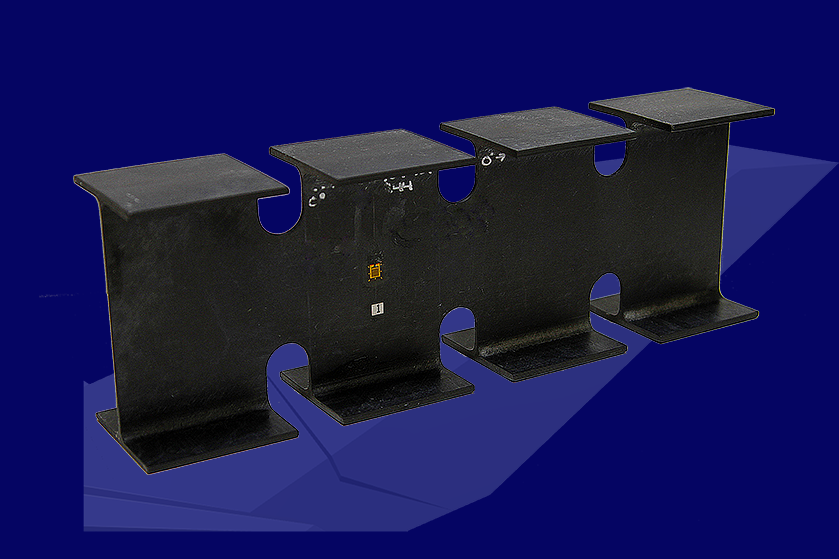
-AS4/PEEK structural load testing
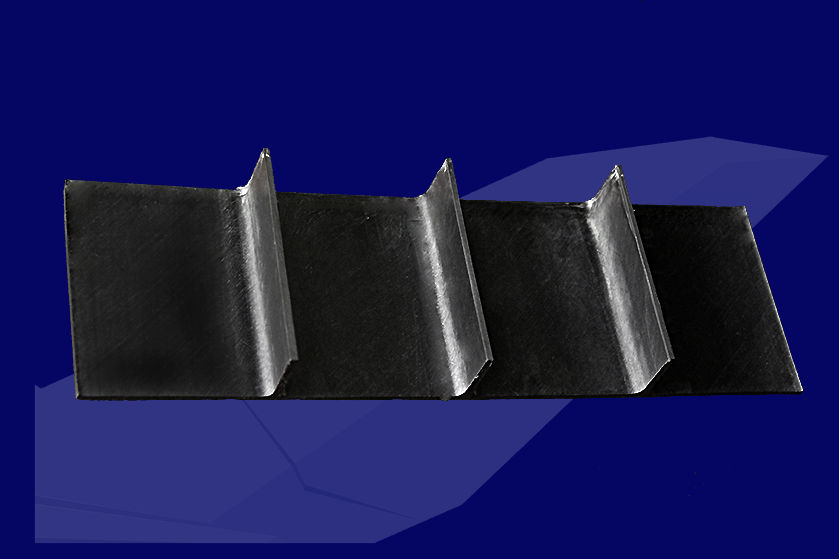
- AS4/PEEK structural load test article
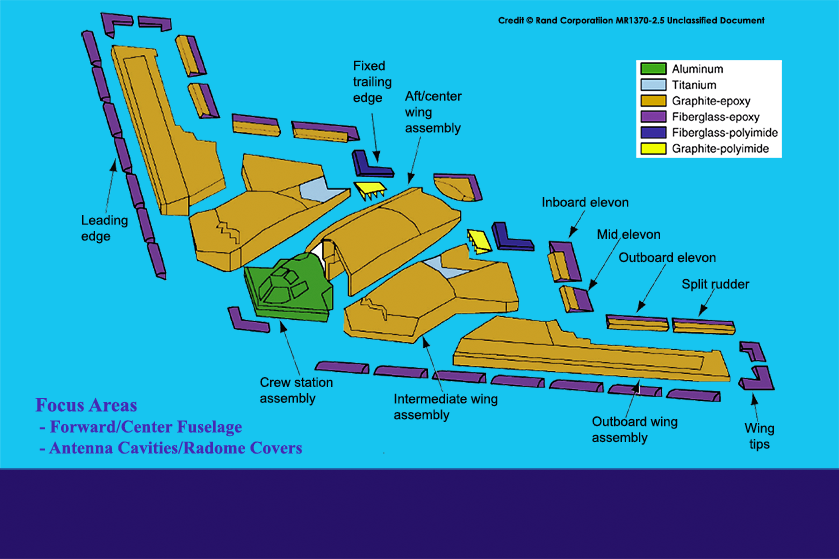

-continuous high modulus fiber orientation / precursor to Z-pin systems
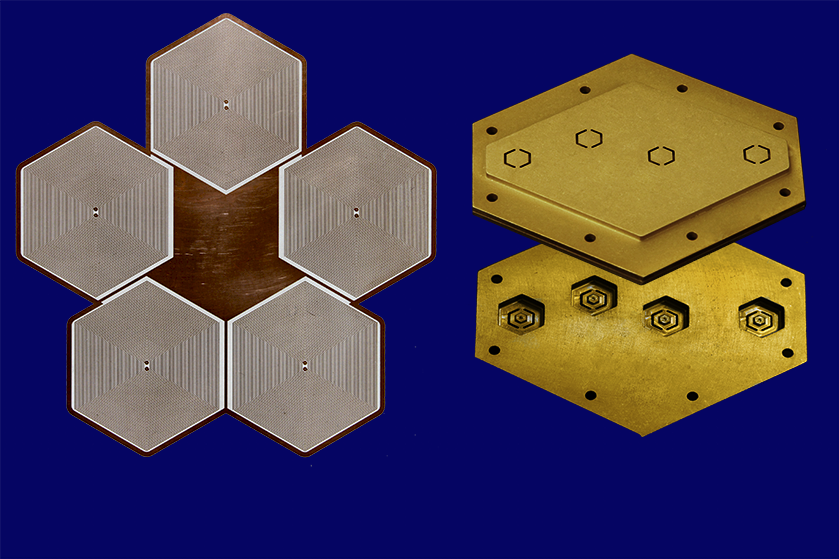
- GPS/X-band element/cavity/radome mechanical design engineering
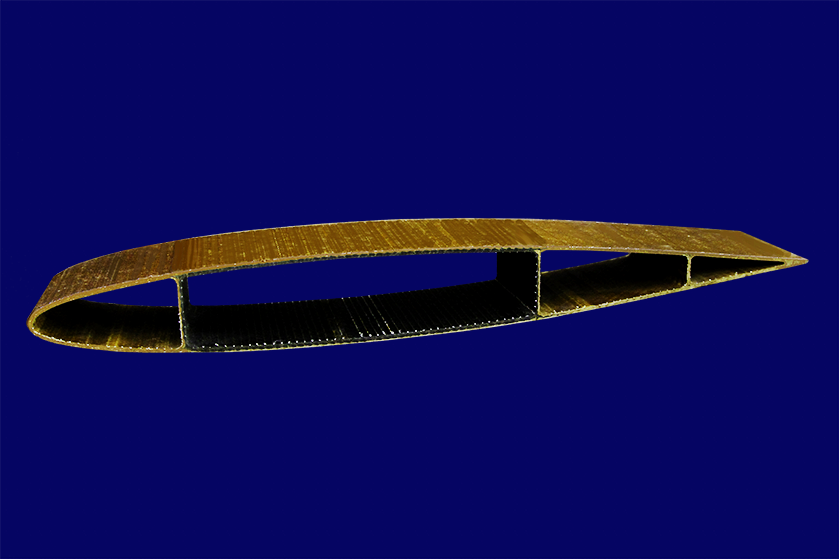
- CFRP / KFRP / GFRP co-laminated air frame structures
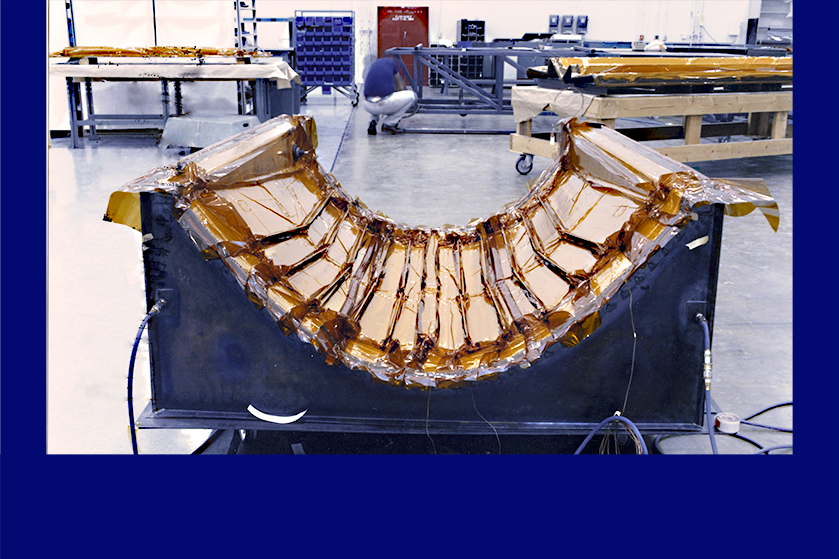
- self heated co-curing of integrally stiffened skin

-b-stage pre-forming for co-curing
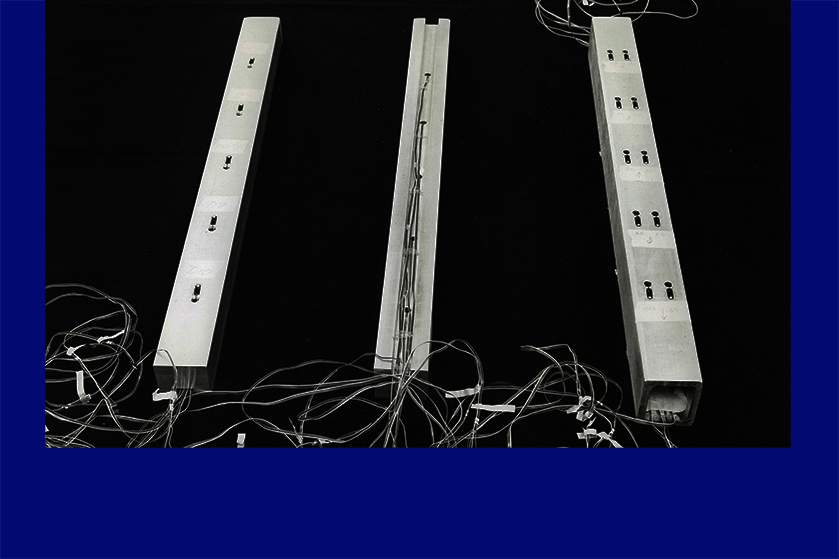
-sensor based internal pressure application
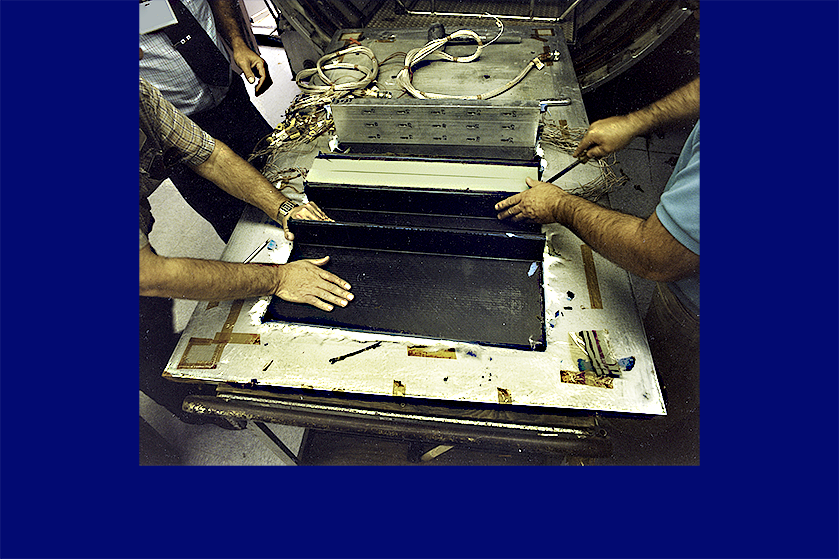
-directional / adjustable pressure curing system
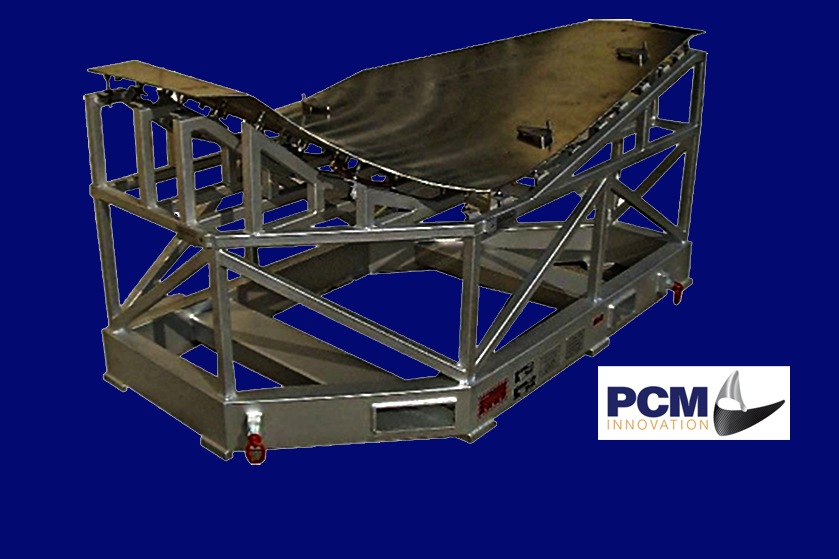
- typical PCM design used on more intricate shapes than shown
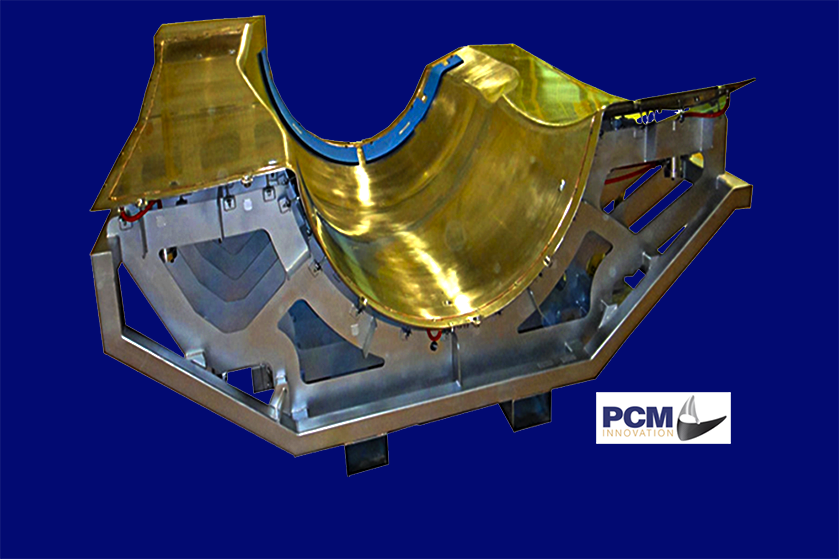
- example of tool type used for tighter lofted fuselage shapes

-self heating ceramic / vacuum diaphragm press forming
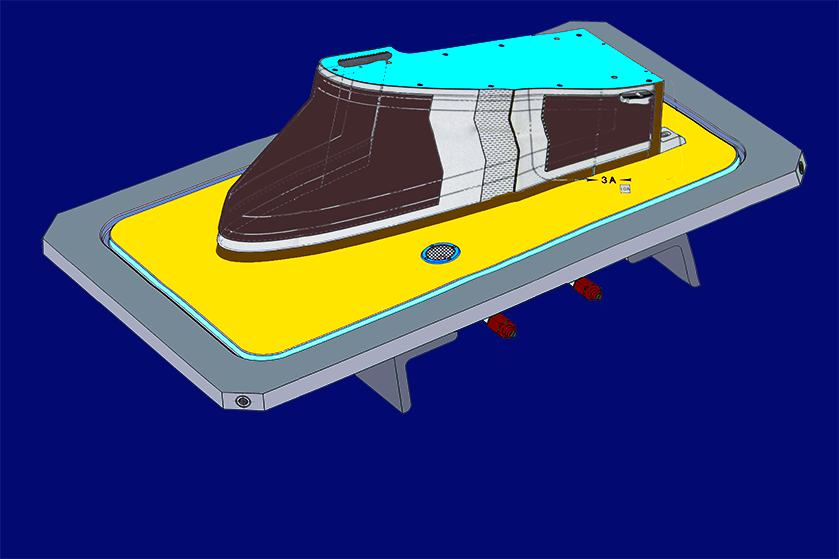
-vacuum assisted resin transfer molding + reusable vacuum bagging
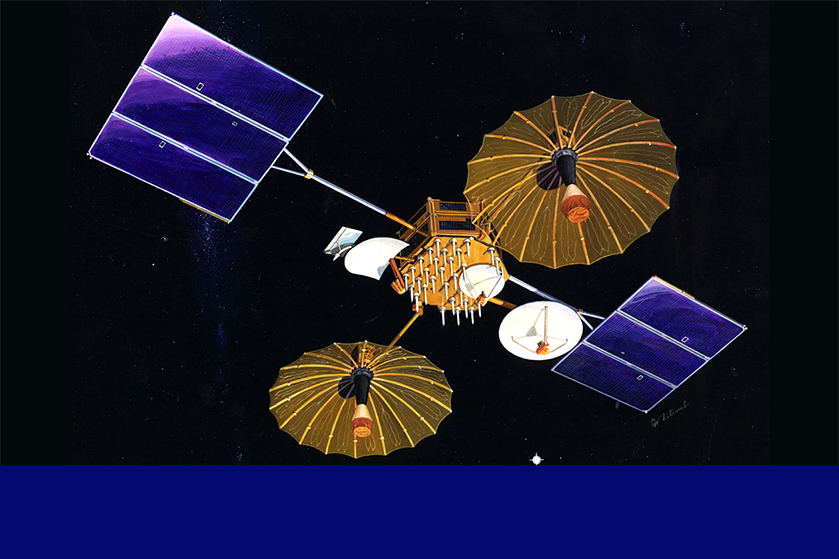
-integration troubleshooting/enhancement

-dual S/Ku band single access unfurlable mesh

- CR&D Lightweight structures program

-pre-flight check at KSC Launch Complex 39-B
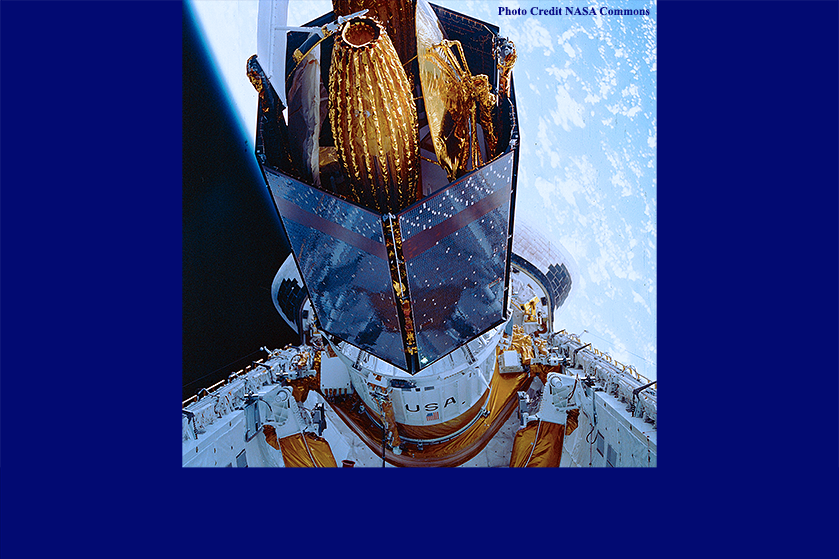
-stowed 5m antenna close up (gold kapton)
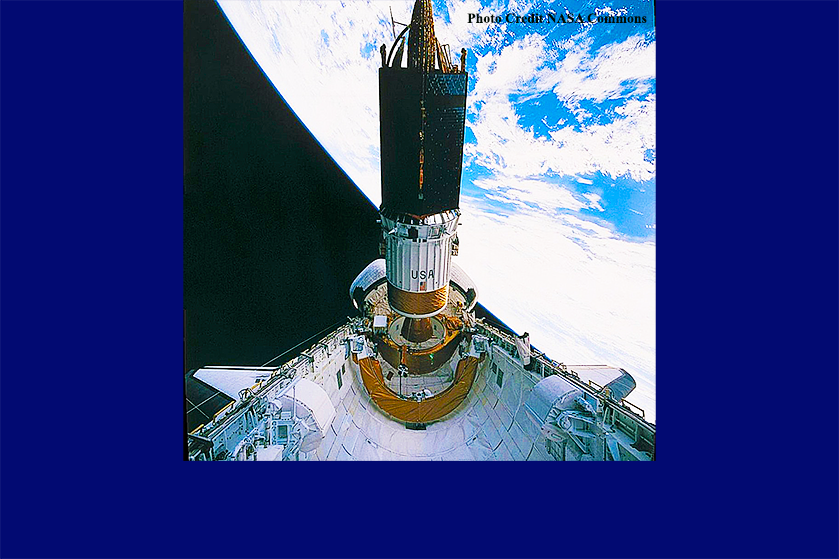
- 5m folded mesh antenna pair at top

- similar to the DARPA Phoenix illustration shown

-metallic mesh/GFRP structural member innovation

Titan 4 Centaur T - KSC Launch Complex 40
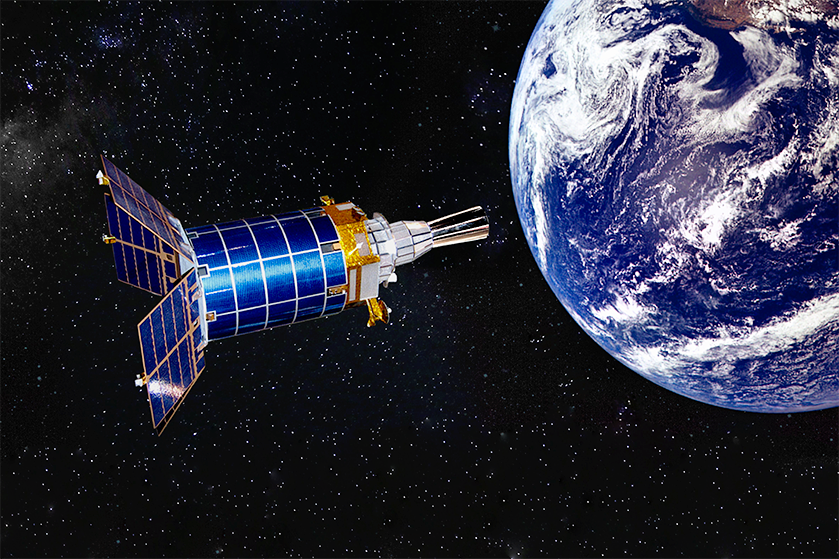
- deployed by STS-44 mission from KSC Launch Complex 39A

-looking at center infrared imaging sensor tube
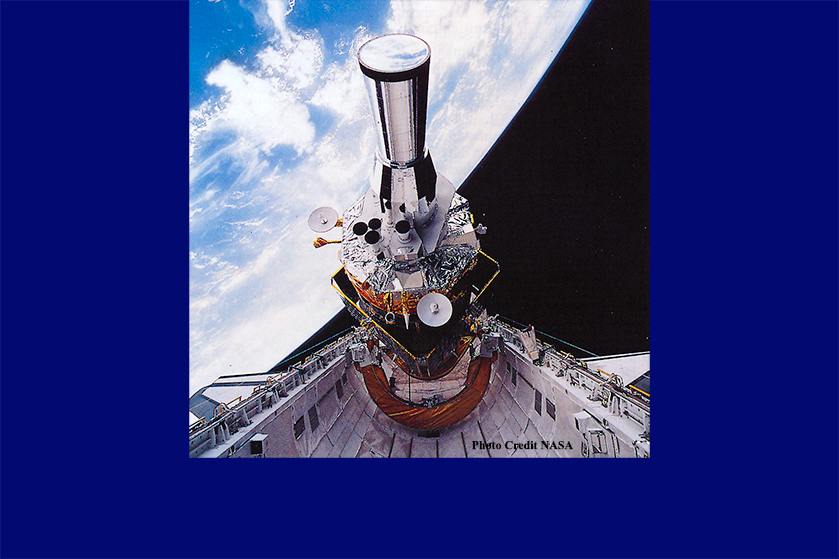
-deployment stage with high gain dish in center
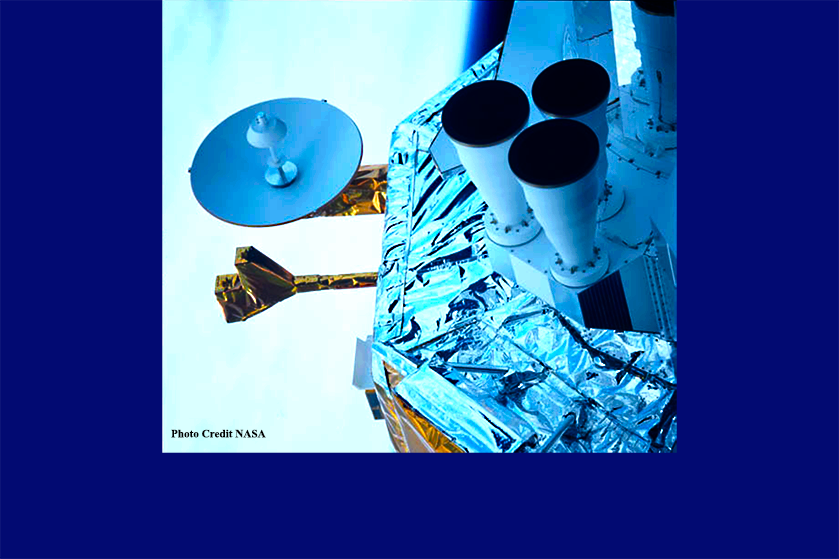
-fabrication, assembly, adjustment and test

- fabrication and assembly

-parabolic antenna feed curvature
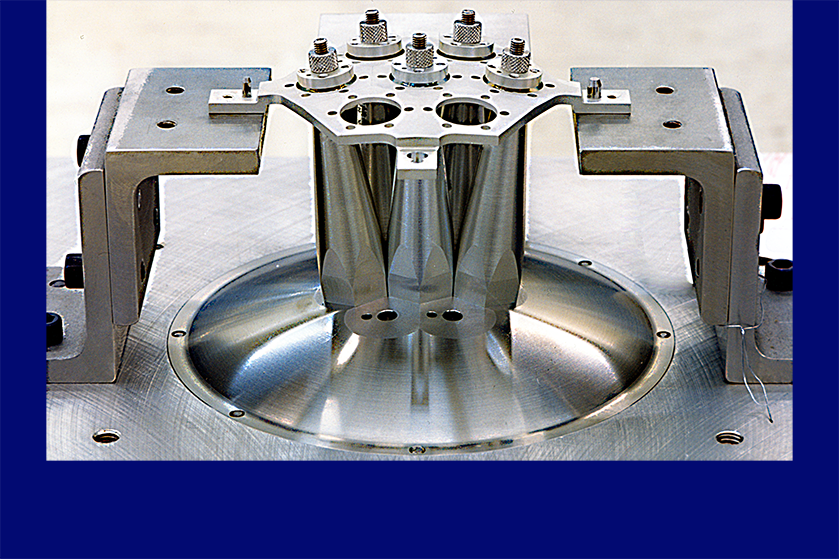


-co-cured assembly
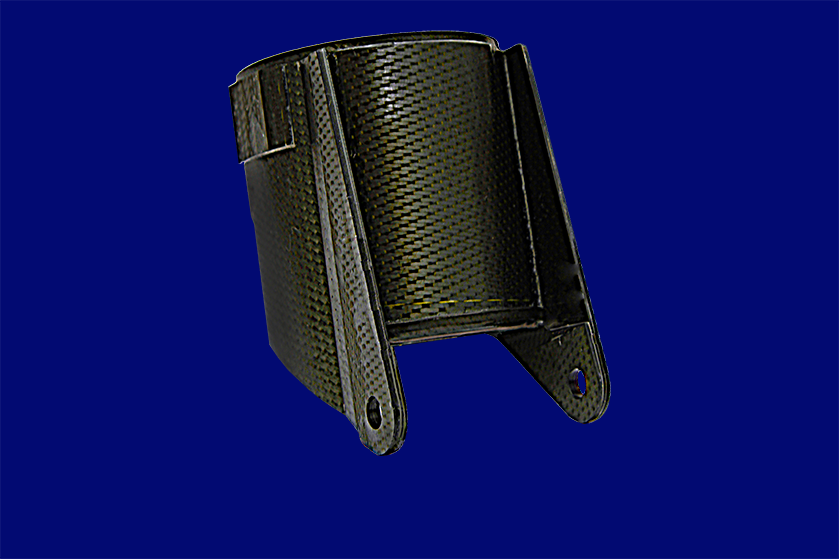
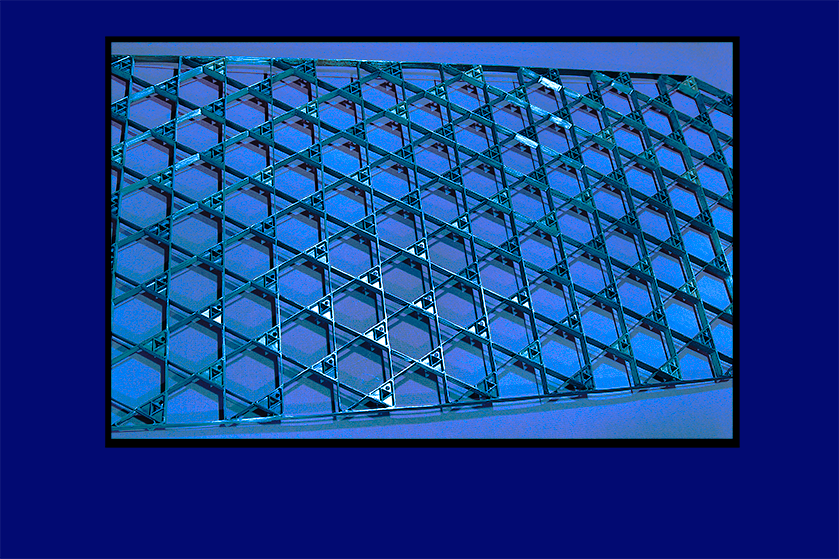
- unidirectional/continuous graphite fiber

-lightweight satellite structures program

-kevlar/graphite spacecraft bus corner
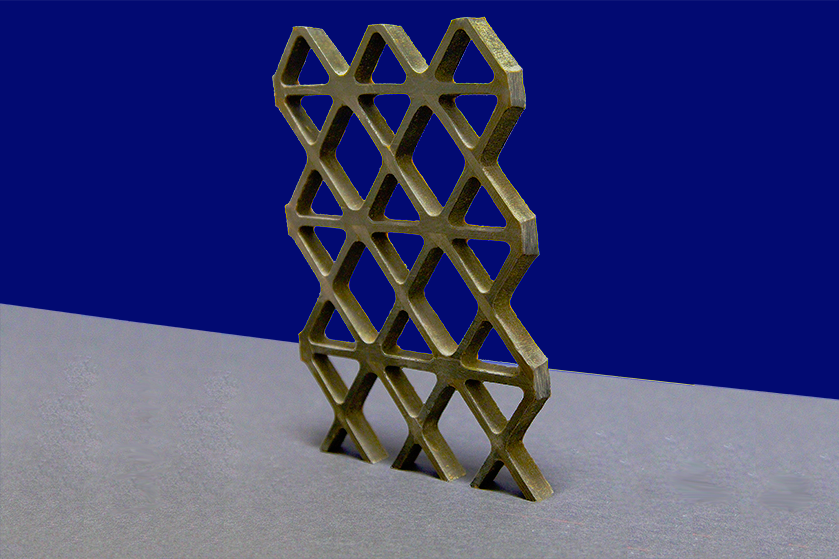
- unidirectional/continuous fiber rtm processed

composite tape placement process development

- 3 variant fabrication time = 1 unit conventional fabrication

- hybrid mfg using simultaneous additive/subtractive steps

integral cooling channels - directed energy deposition
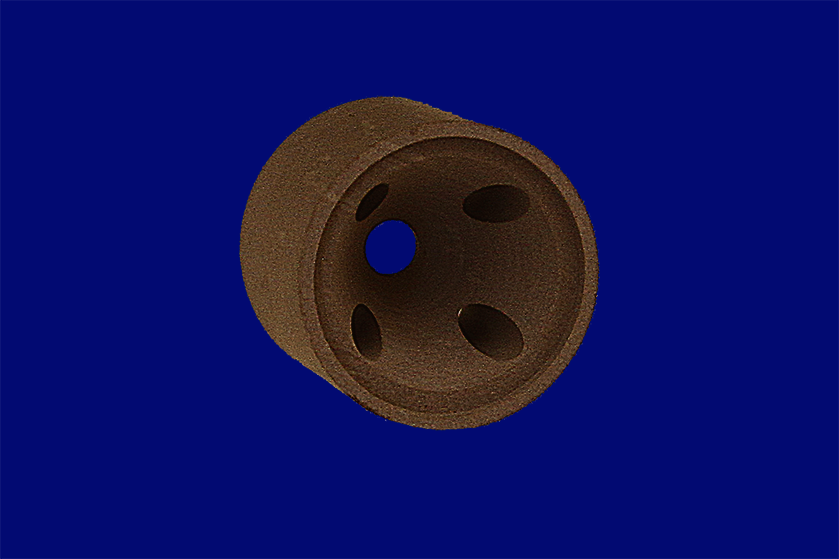
- directed energy deposition / minimal machining

-mandrel based sintering

short fiber nozzle extrusion with final mold compression






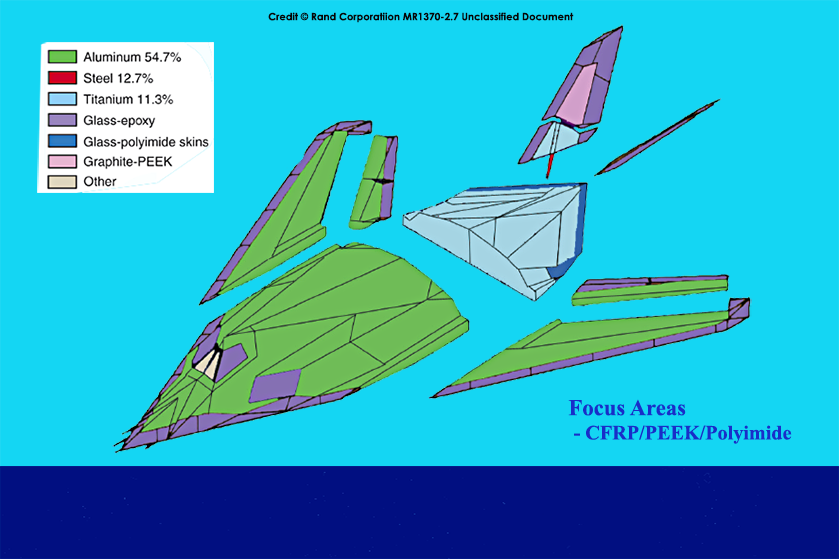
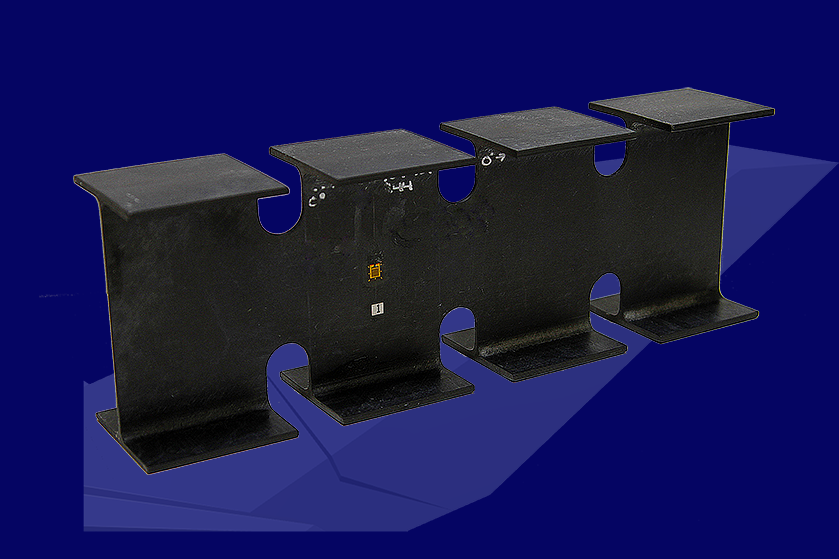
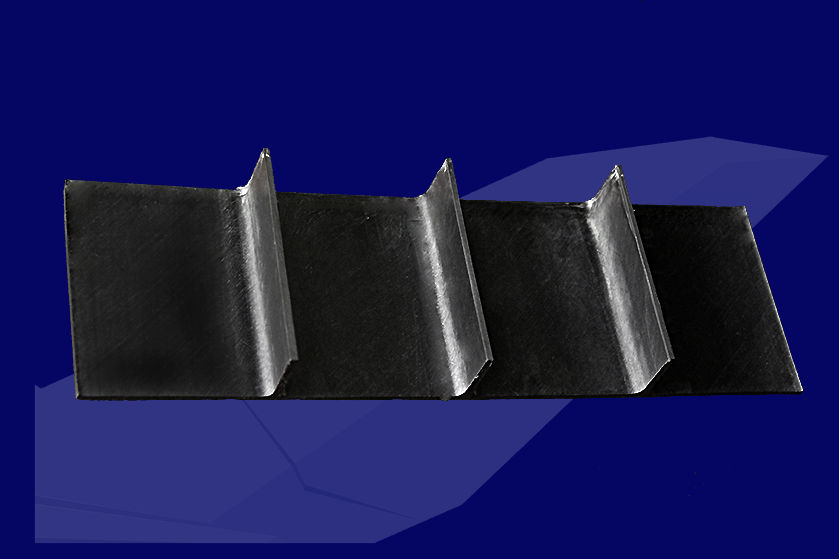
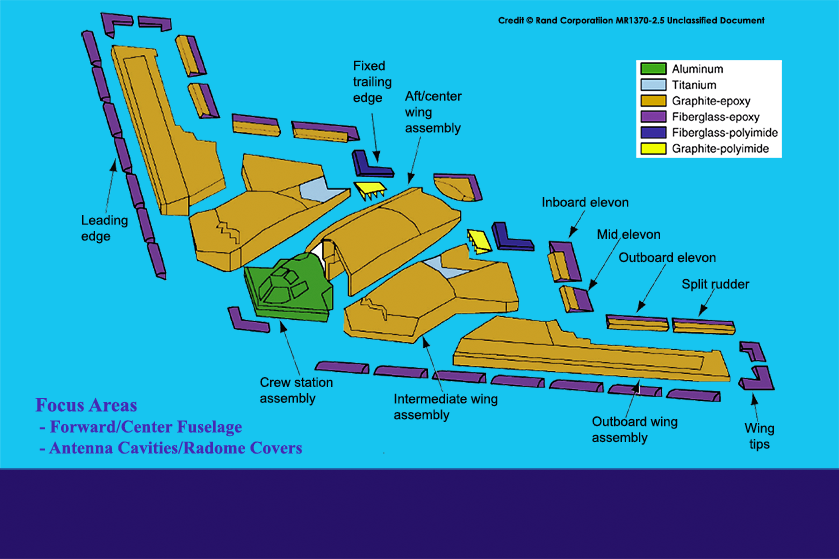

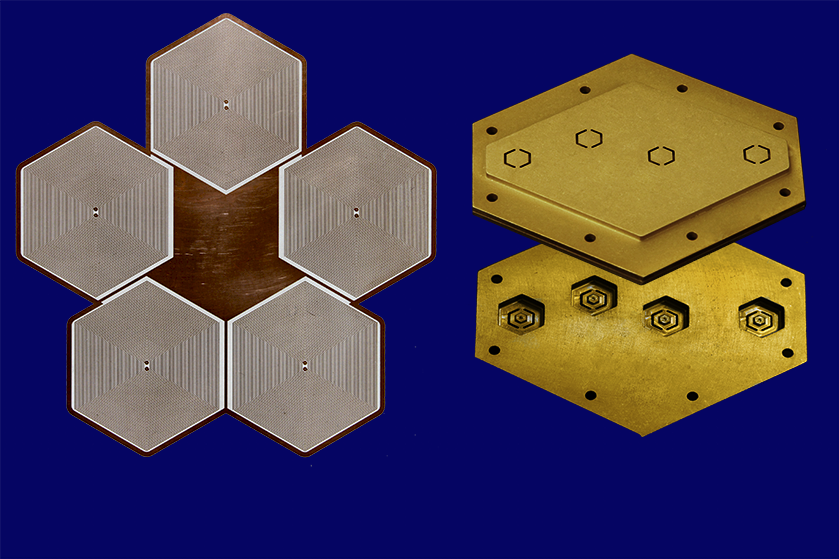
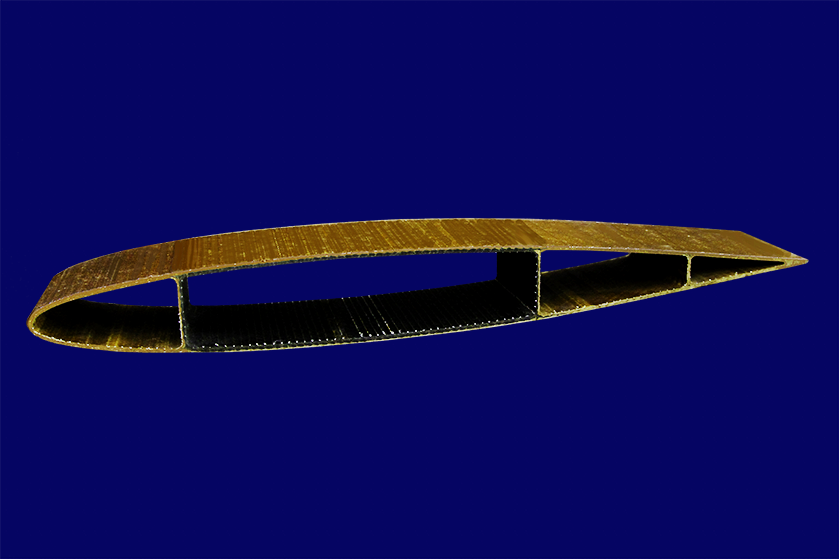
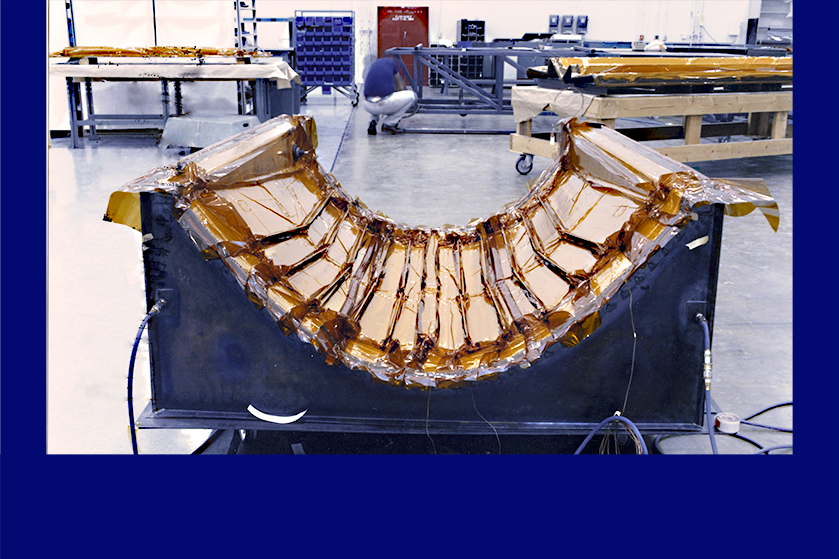

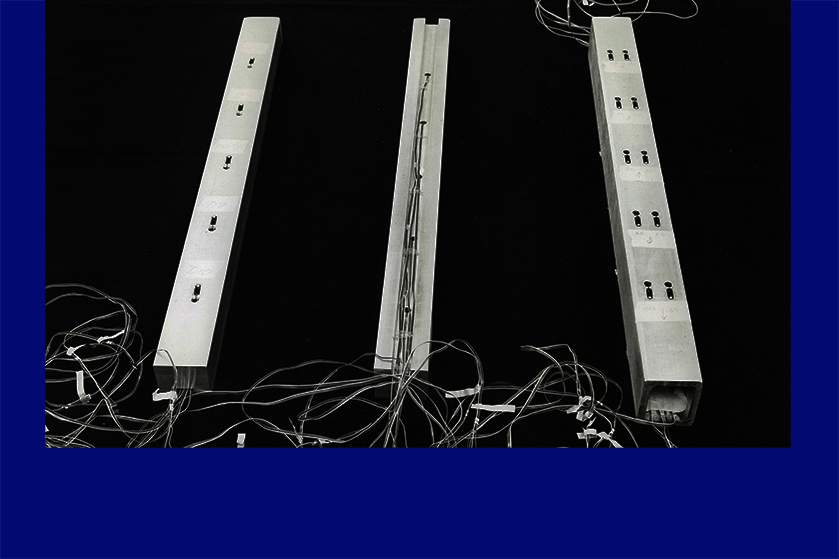
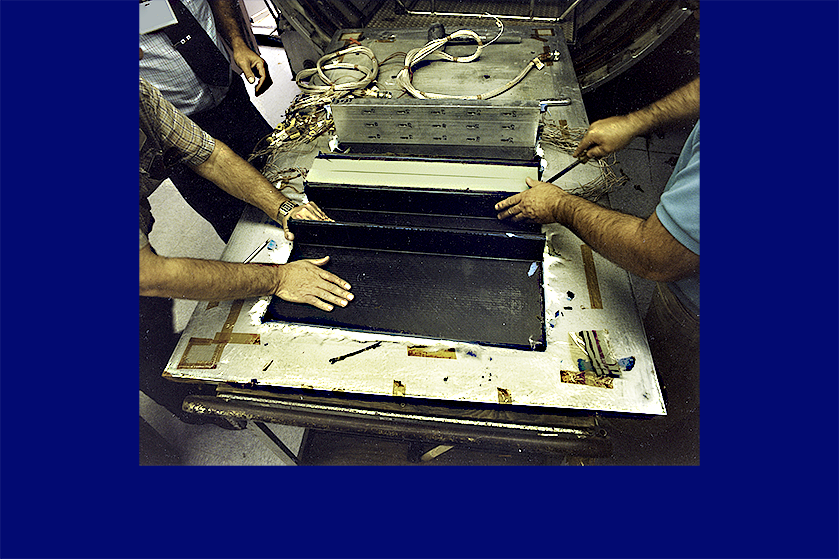
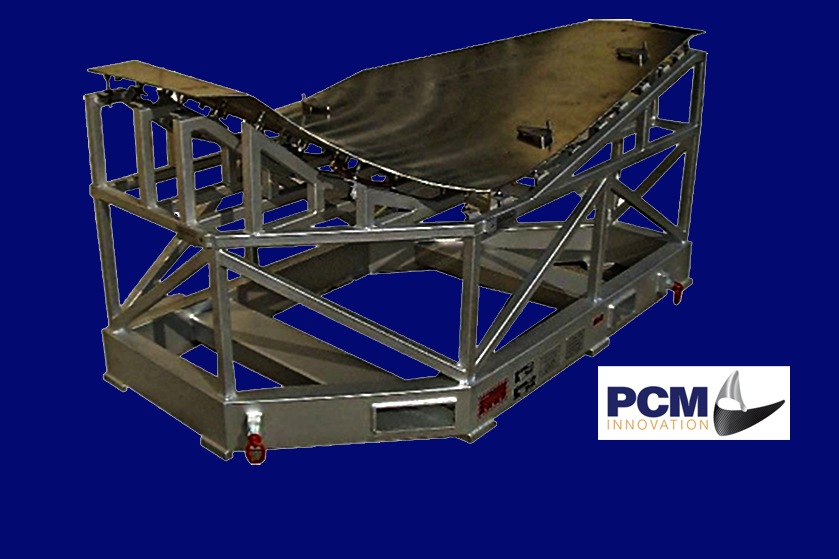
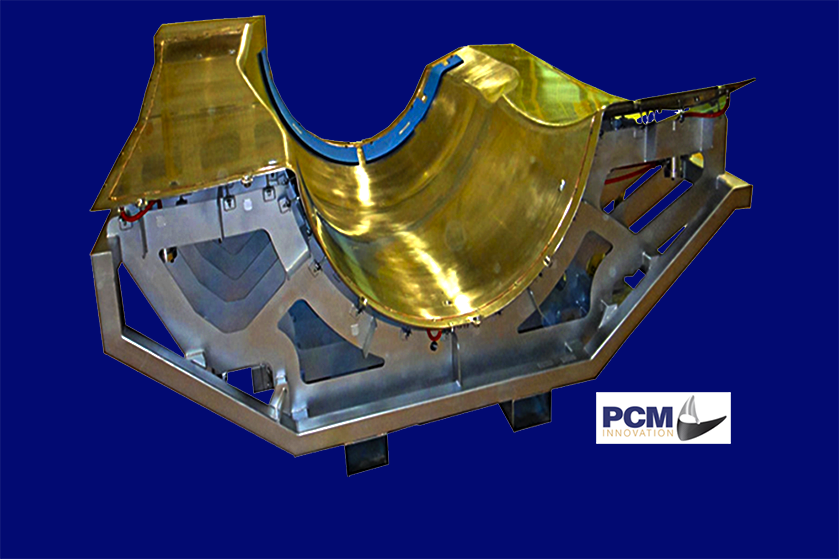

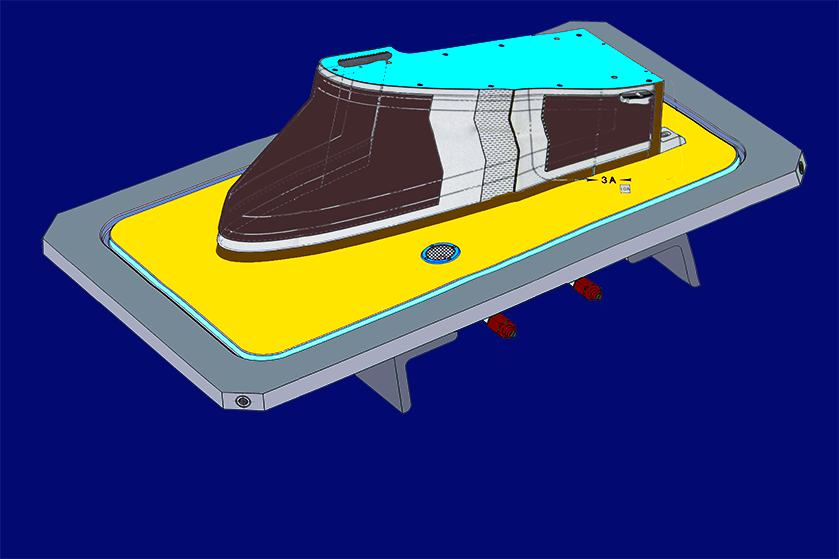
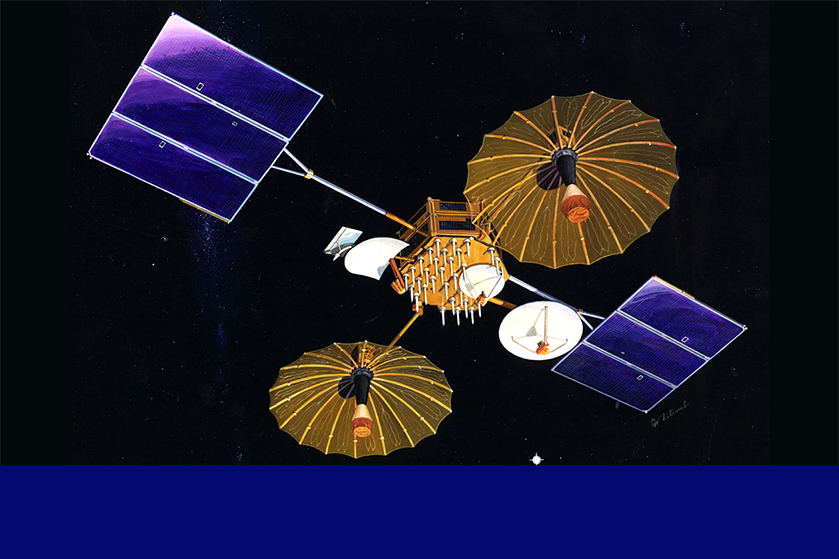



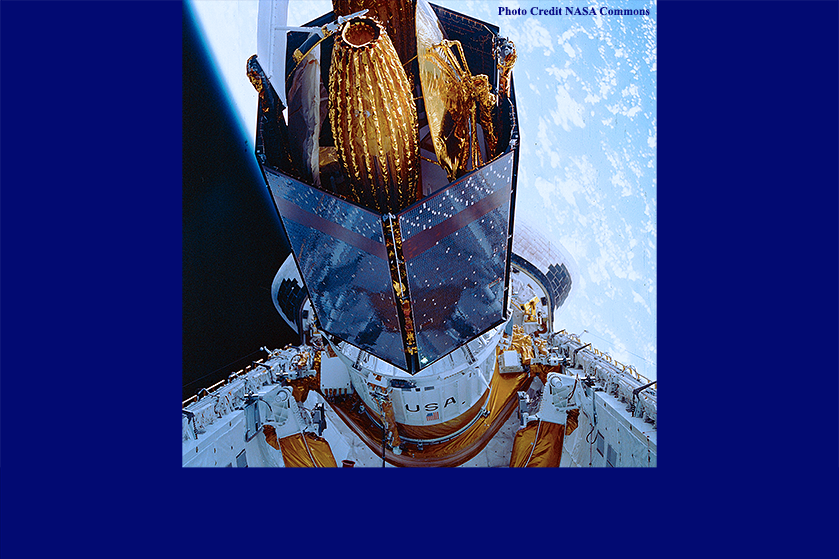
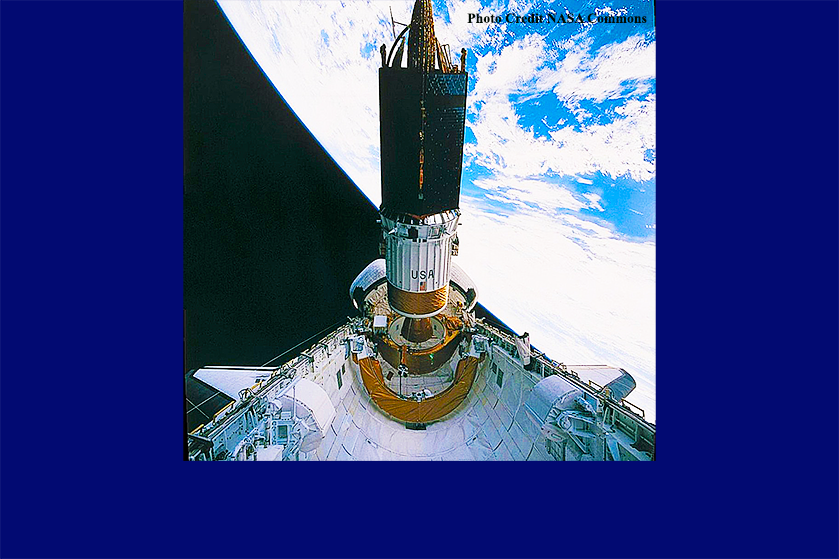



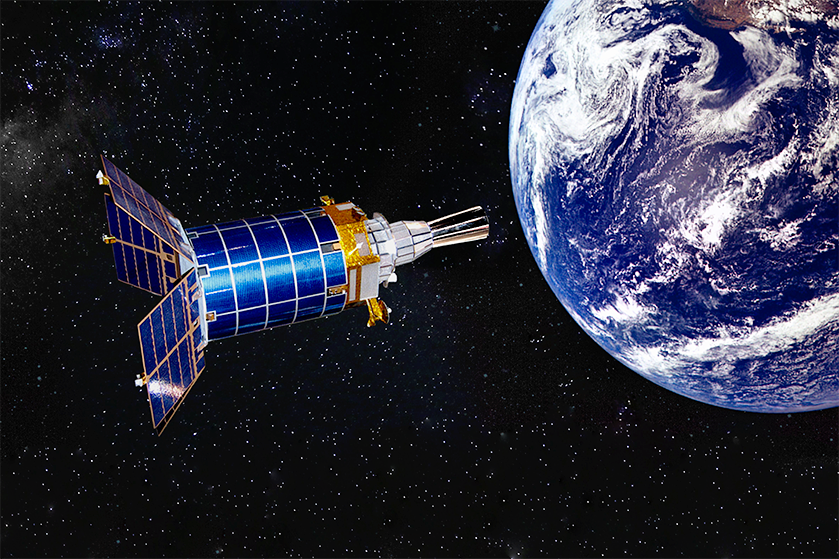

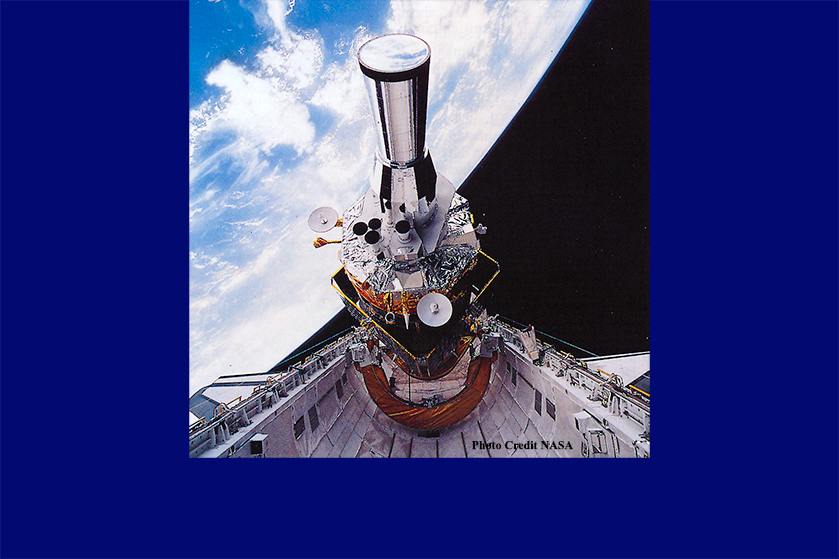
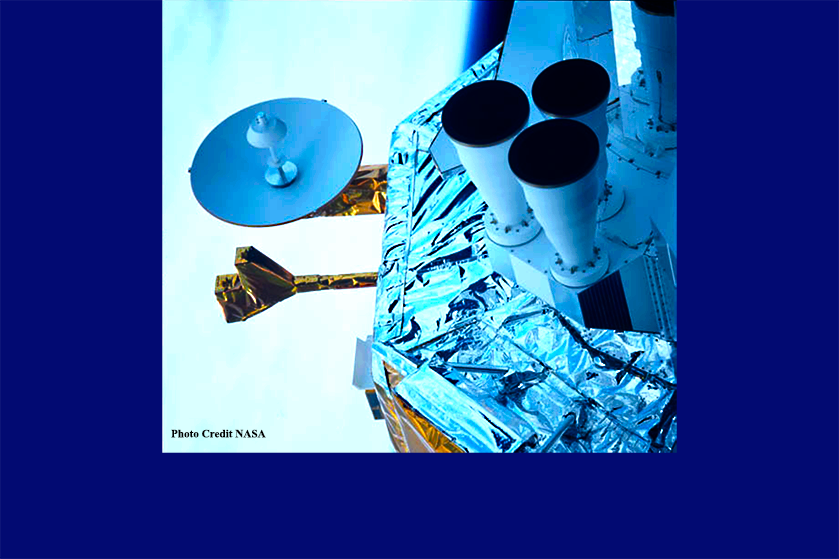


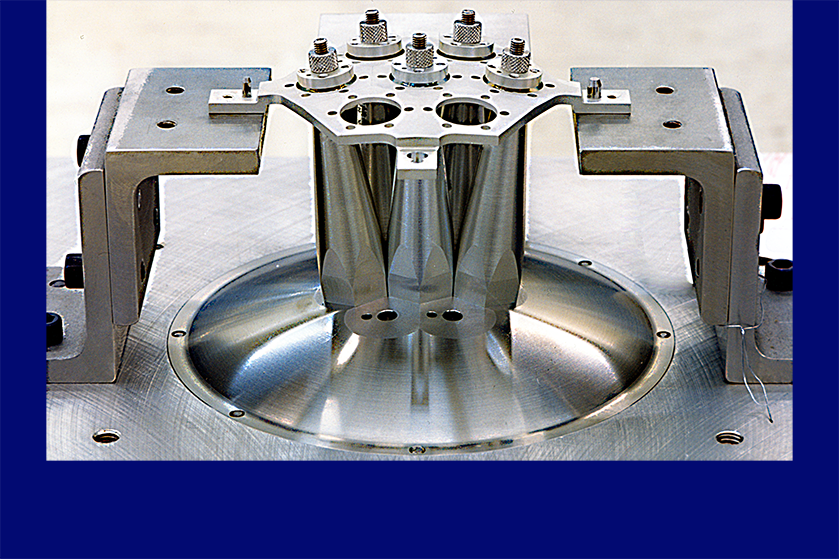


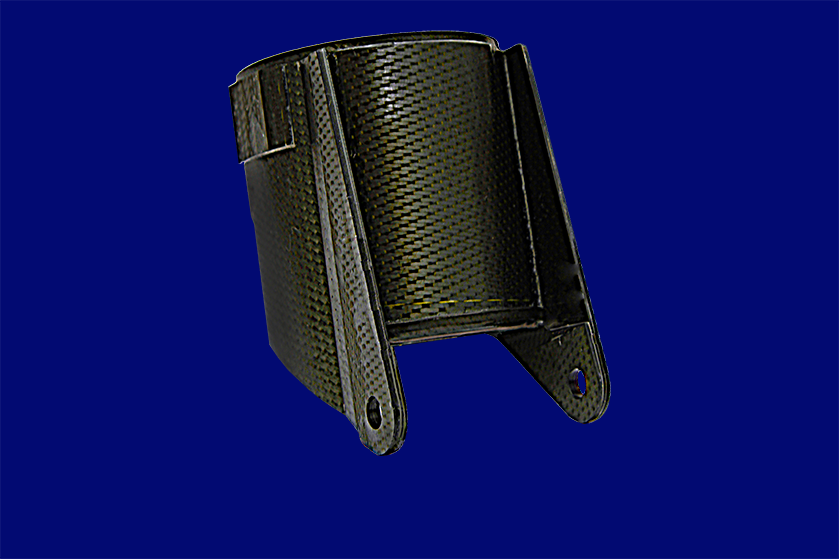
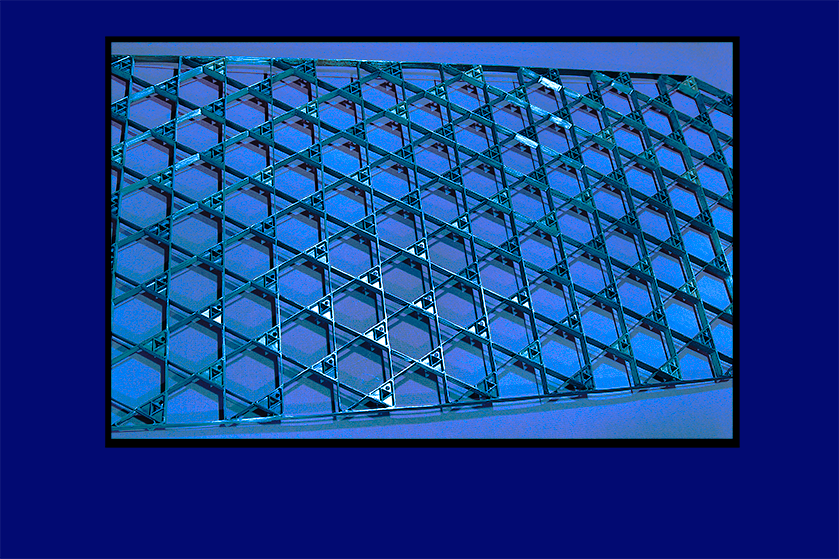


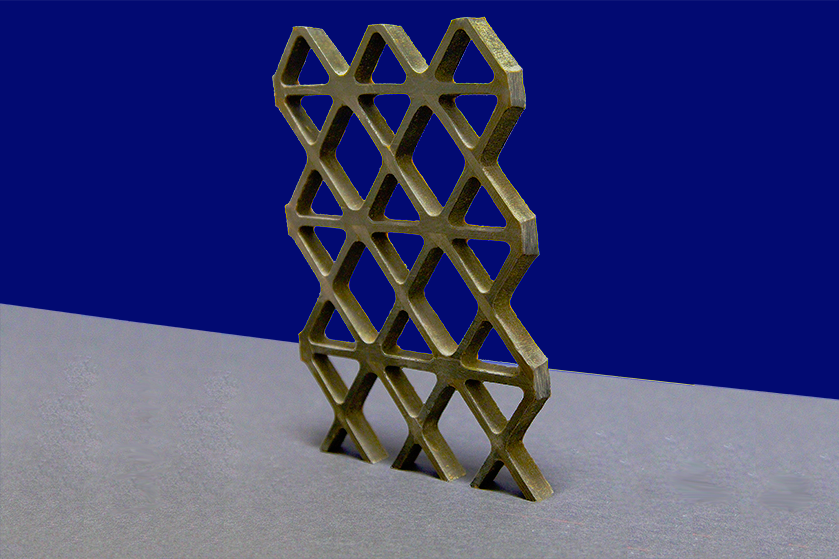




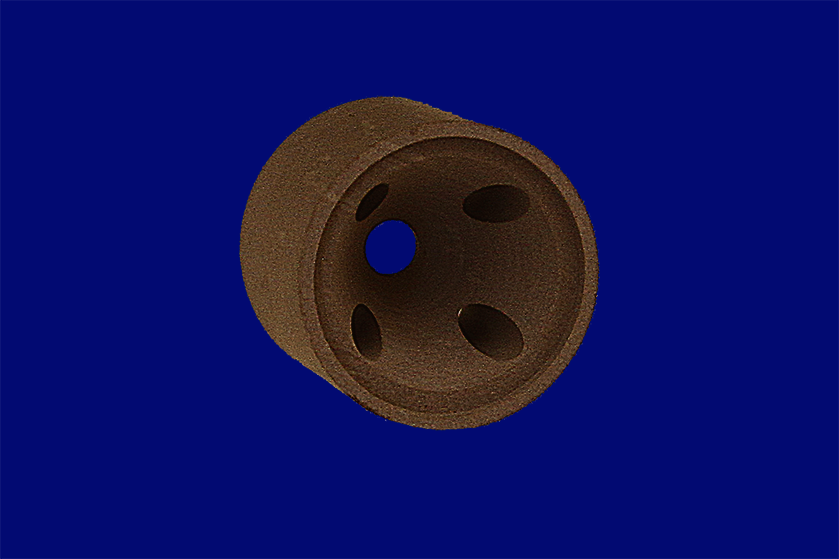

