Nuclear Energy Projects - Fusion magnet R&D, manufacturing, tooling and assembly
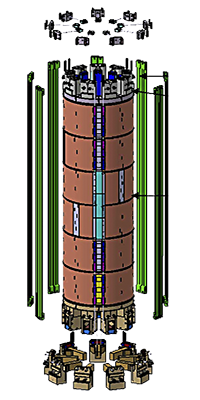
The ITER Central Solenoid - a stack of (6) magnet modules
The ITER Central Solenoid - building the world’s largest, most powerful pulsed magnet
Built and tested in the U.S. by General Atomics
made of (6) stacked, 110 ton module sections
diameter = 4.25 meters/14 feet
assembly height = 18 meters/59 feet
assembly weight = 1000 metric tons/1100 U.S. tons
length of coiled superconductor = 21 miles/33.6 km
magnetic field strength = 13 Tesla (280,000 x earth’s)
can lift a 100,000 ton aircraft carrier
operating drive current = 15 million amperes
operates at 4.2 °K / -269 °C


- final home for the 1000 tonne Central Solenoid (CS) magnet

- developed for build access to magnet top/bottom (167 tons in rotation)
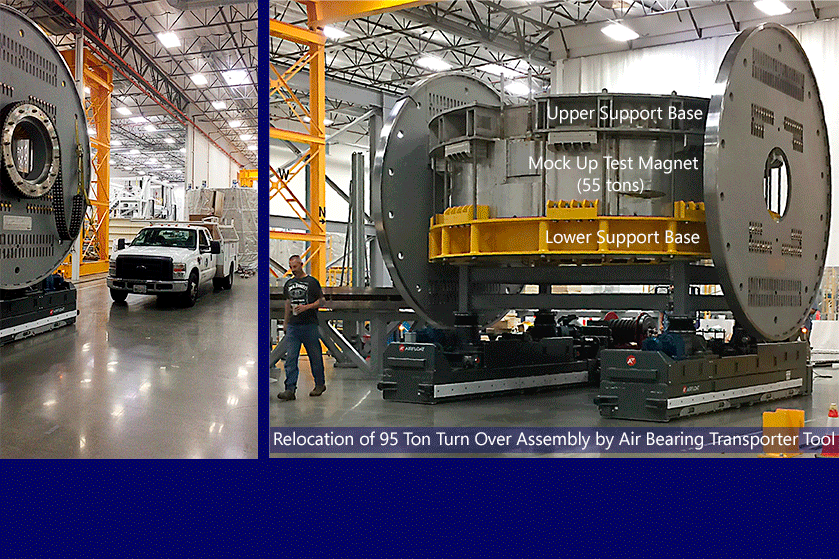
- moving the 55 ton test magnet with an air bearing transporter
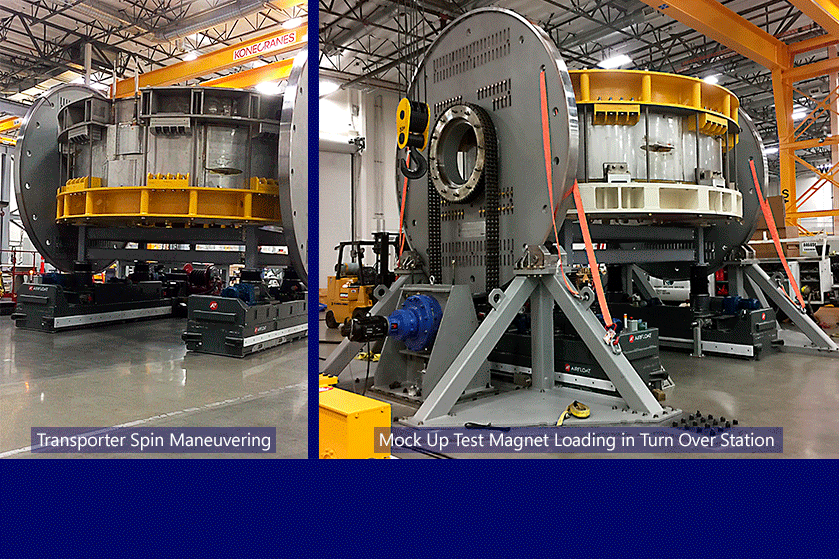
- 55 ton test magnet part of 102 ton rotating assembly

- 102 ton rotating assembly ready for turn over

- 55 ton test magnet/102 tons rotating (qualified with 215 ton payload)

-system can safely stop at any point in the rotation cycle
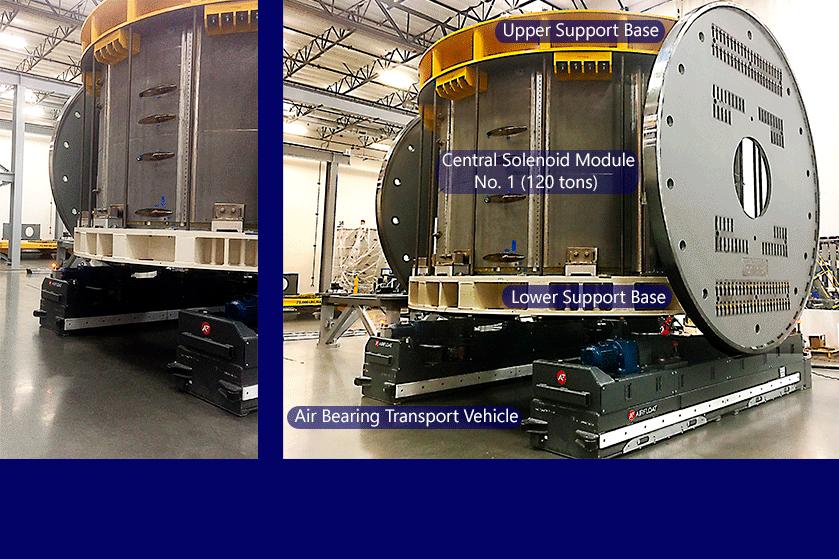
-delivering the first 110 ton CS Module to the turn over tool station
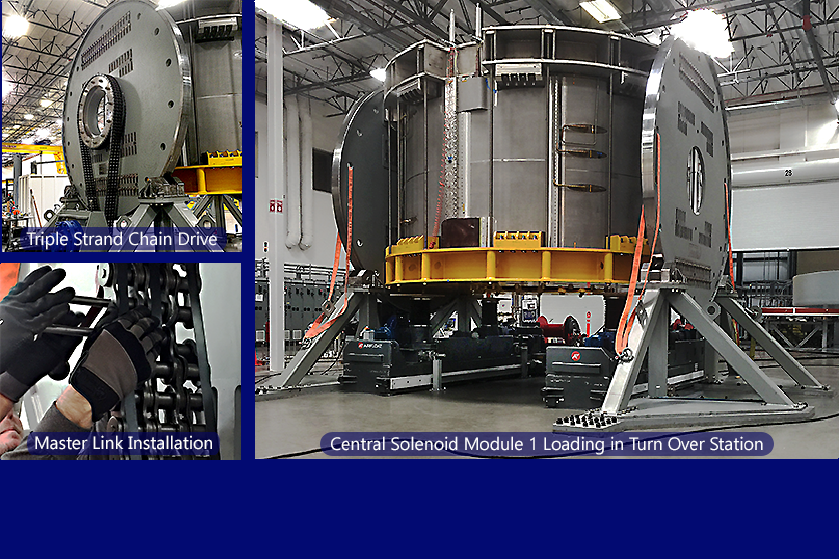
- 120 Ton Central Solenoid magnet part of 167 ton rotating assembly
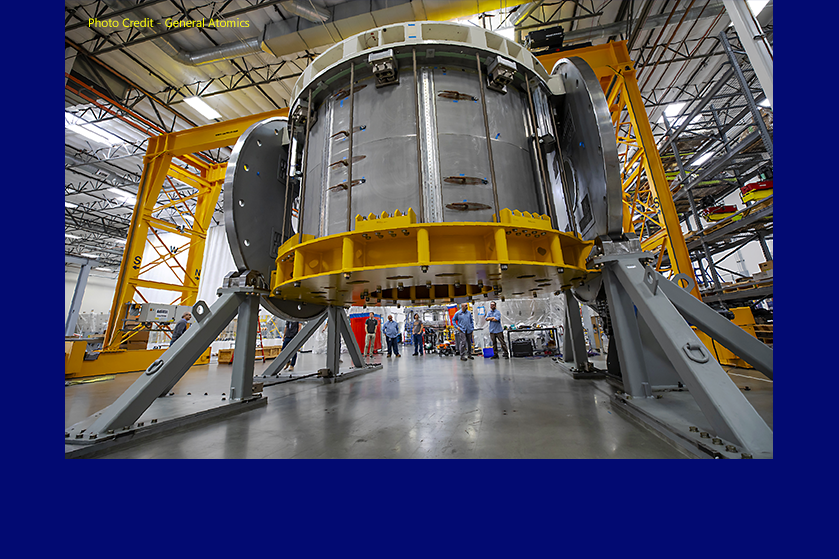
-167 ton rotating assembly ready for turn over
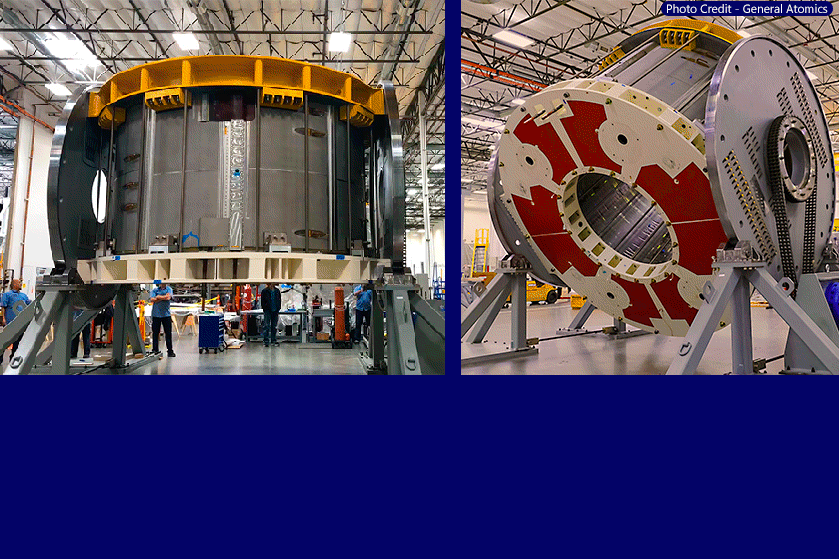
-accelerated 4.5 minute inversion cycle for CS Module 1
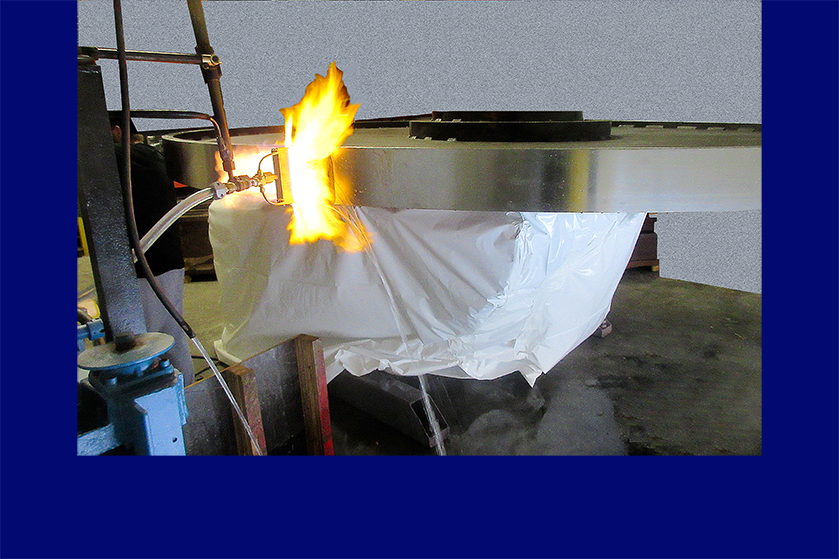

- structural analysis by hand calculation and FEA
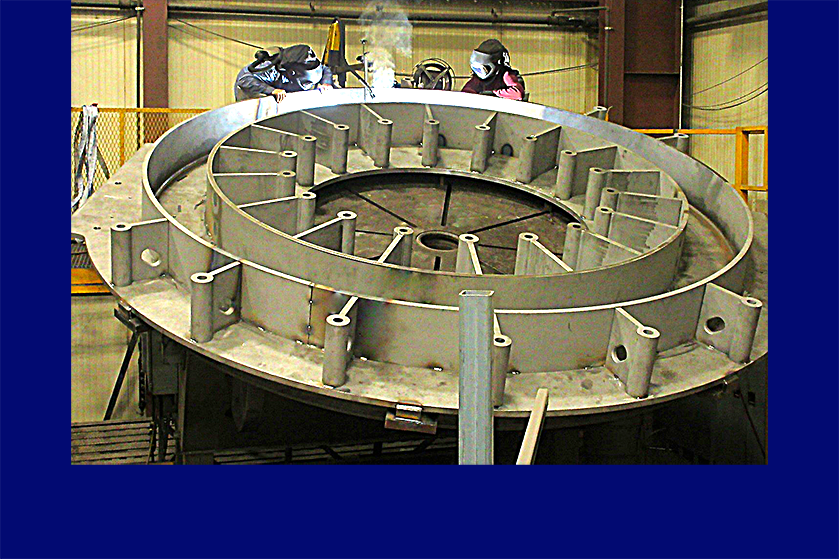
- weld joint sizing/stress analysis

- weld analysis/sizing to Eurocode/ASME lifting stds

- FEA/hand calculated weld sizing for strength vs. low distortion
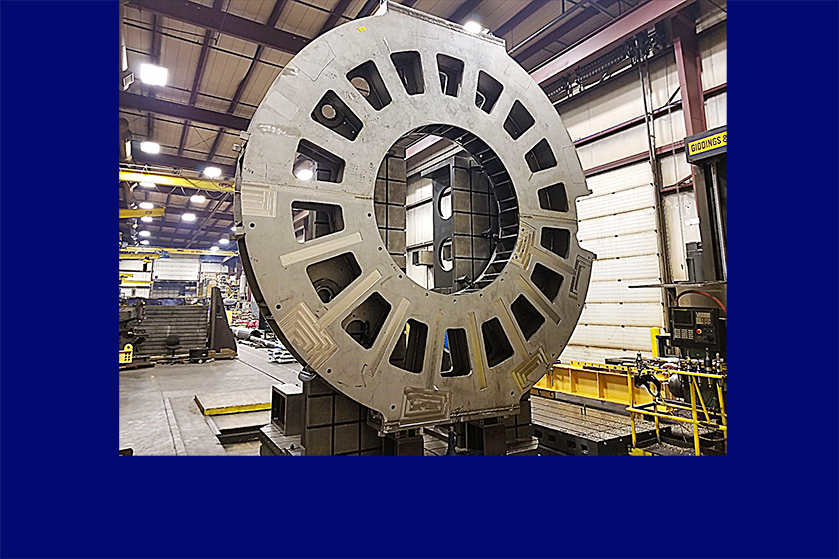
-low thermal mass design for -269 °C service
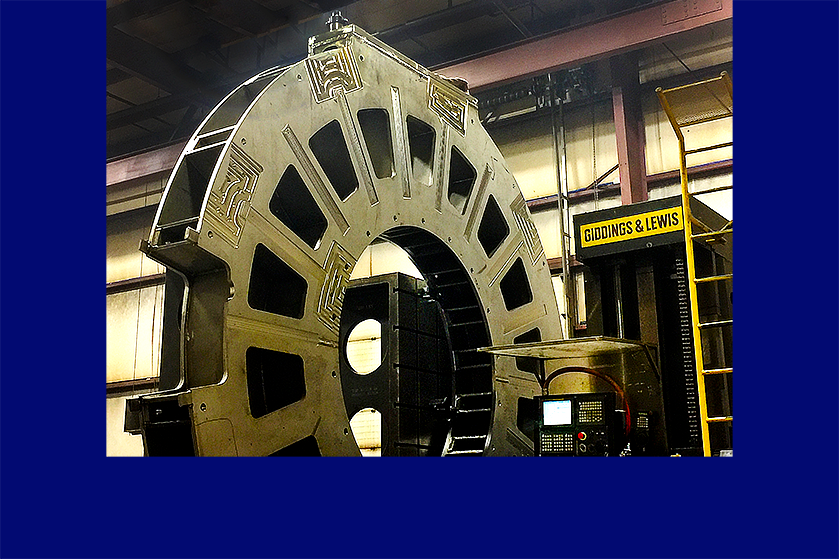
- designed for manufacturing to reduce material removal induced distortion

- thick wall water cooled pipe in vacuum vessel

- completion of final cover/fill pass

- visual check for complete joint penetration
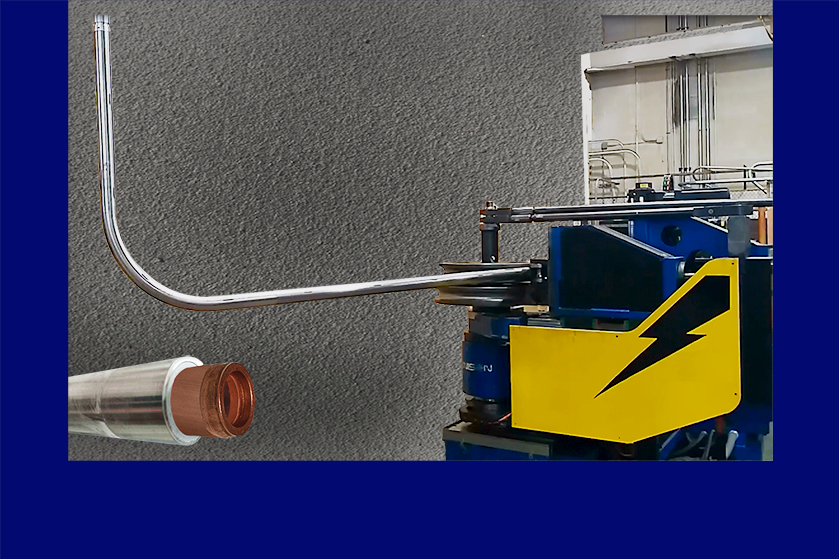
- roll forming compound (spherical) bends ±0.4 mm

- rotary drawing 90° corner bends

- high force electric push bending
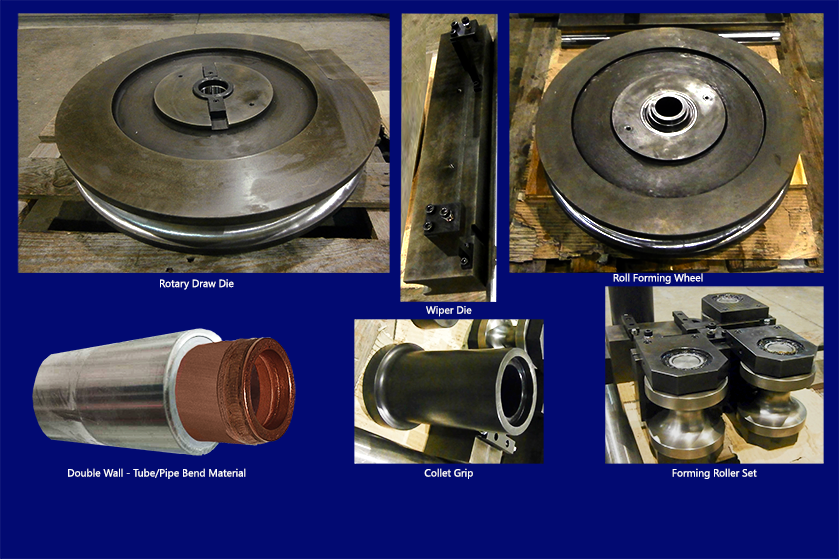
- high force electric push bending
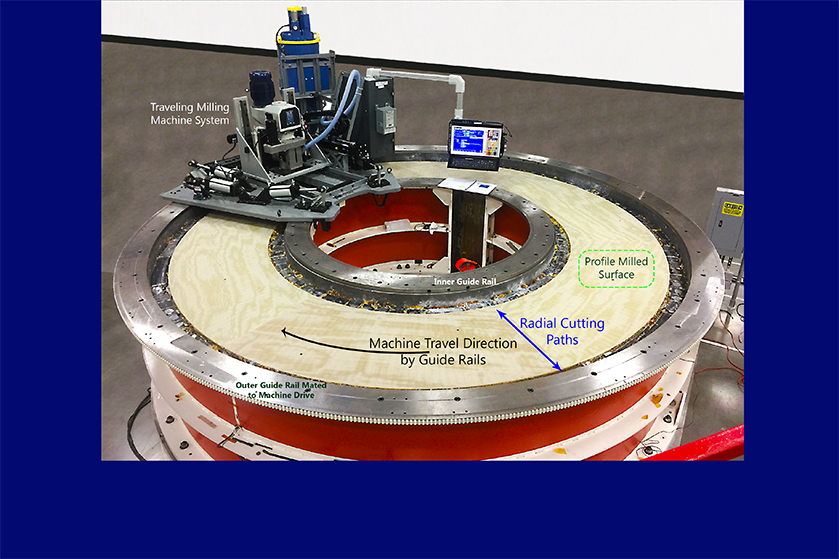
- process/equipment development for 0.5 mm magnet surface parallelism
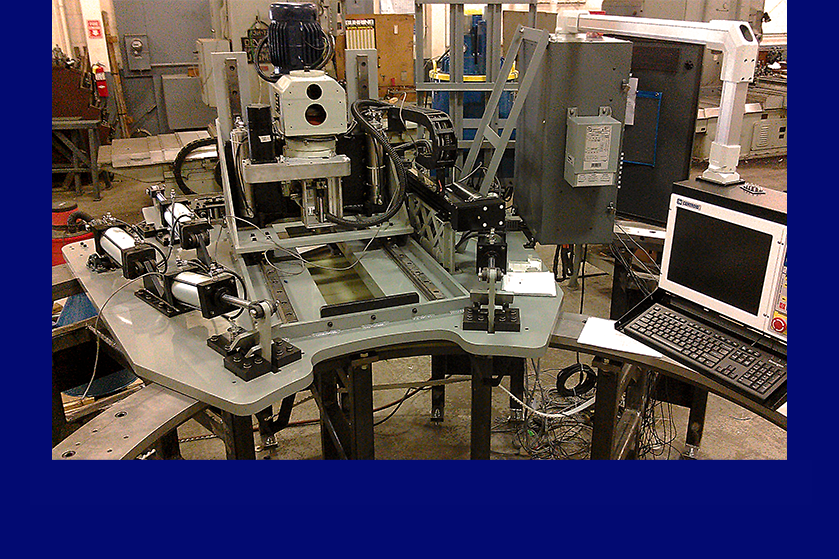
- x/y/z axes + lifting/clamping testing
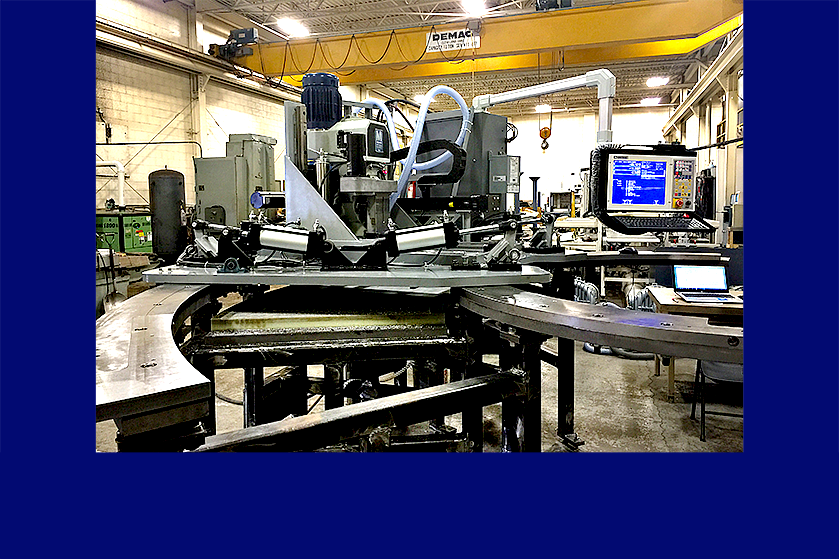
- equipment testing on mock up structure
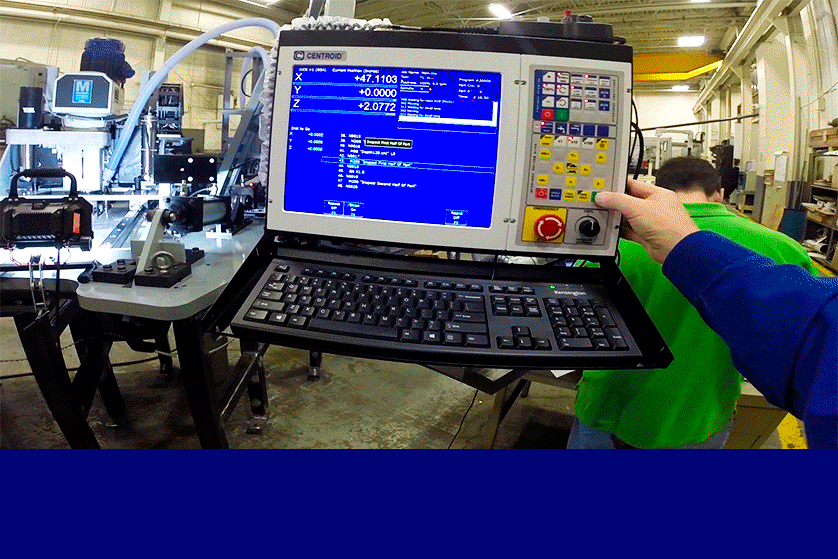
- x axis travel tuning/calibration/qualification testing
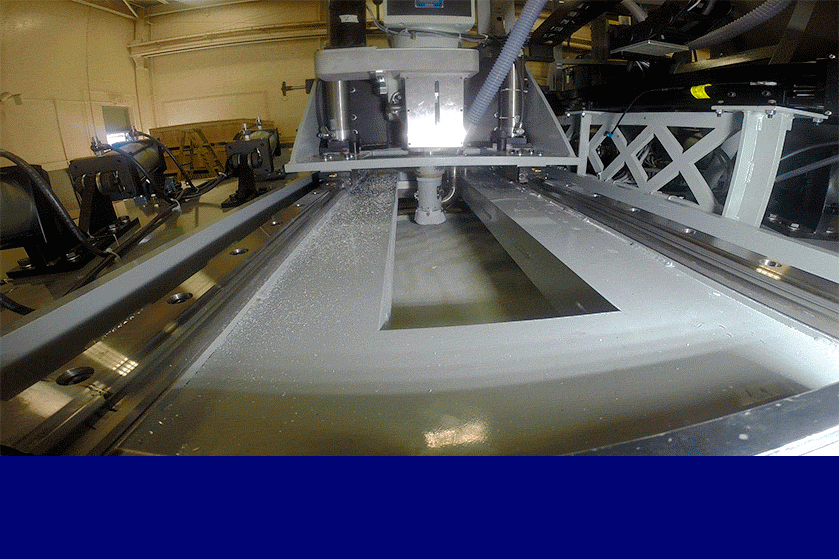
- y + z axes radial cutting spindle testing / tuning / calibration / qualification
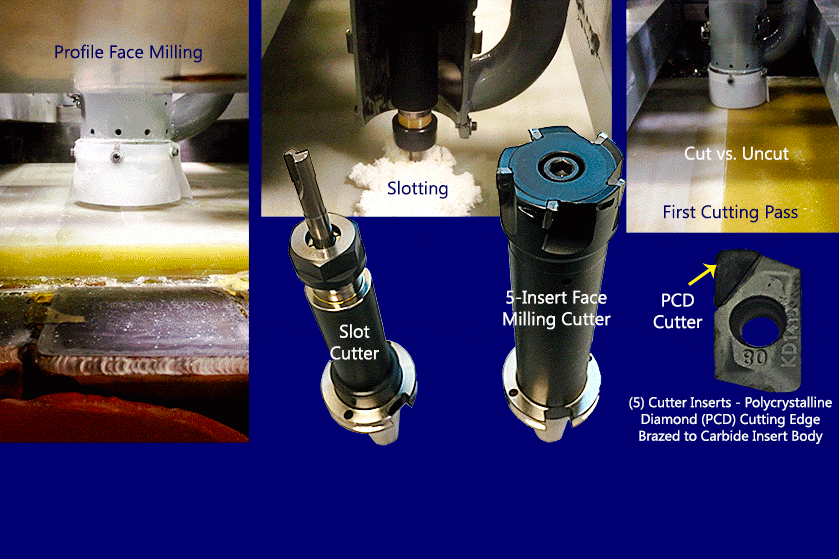
- G10 laminate cutting process development
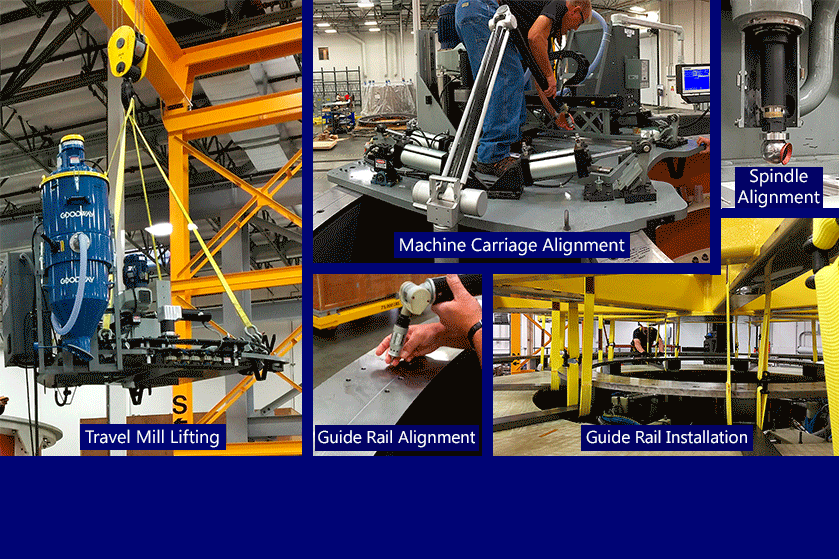
- equipment installation / alignment on magnet top
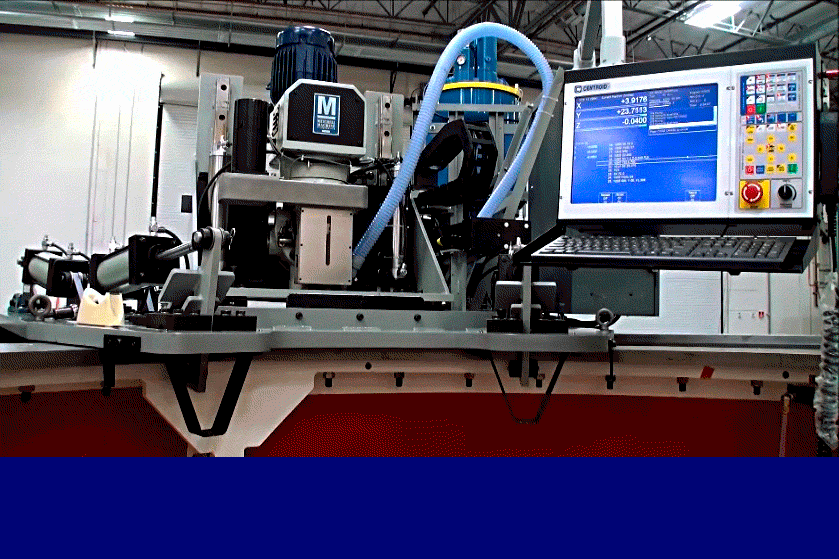
- final CNC programming and validation
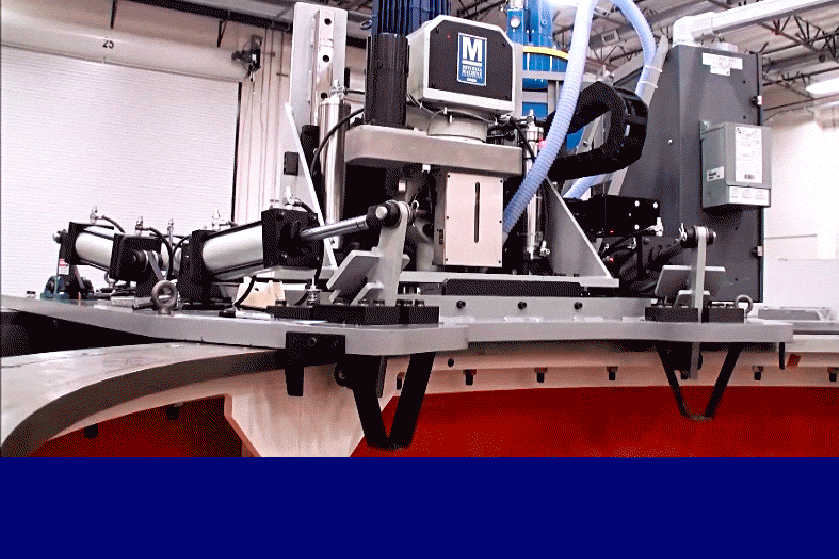
- process & equipment validation / commissioning

- final CS magnet module machined surface profile

- final CS magnet module surface slotting
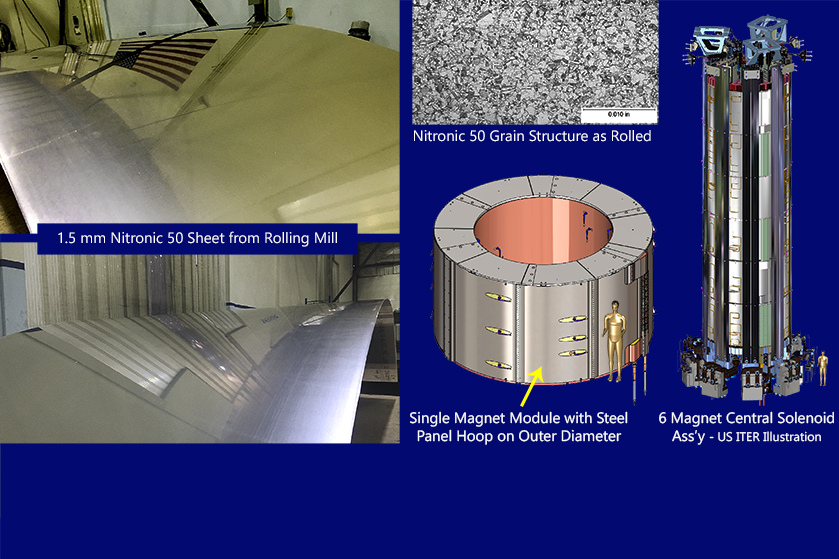
- nitrogen strengthened austenitic steel sheet (Nitronic 50)
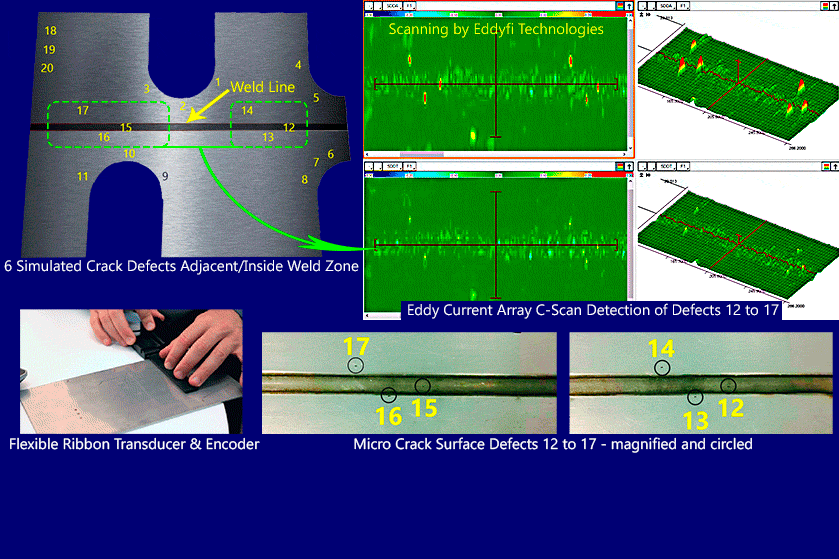
- small defect detection in autogenous welds - 1.5 mm Nitronic 50 sheet
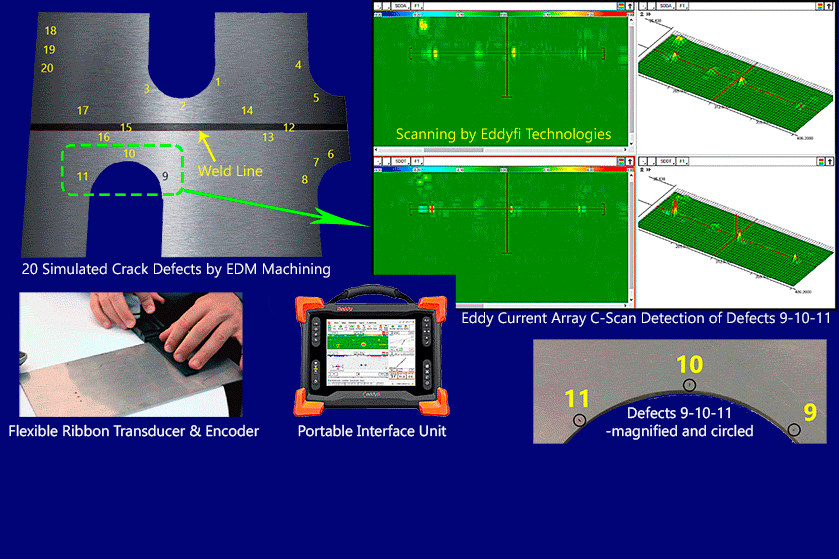
- micro-crack detection in fine grain austenitic sheet (Nitronic 50)
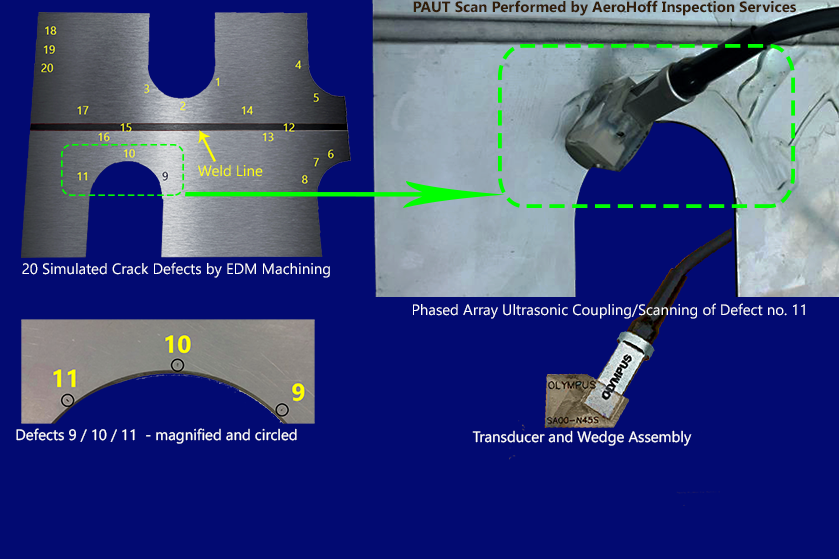
- micro-crack detection in fine grain austenitic sheet (Nitronic 50)
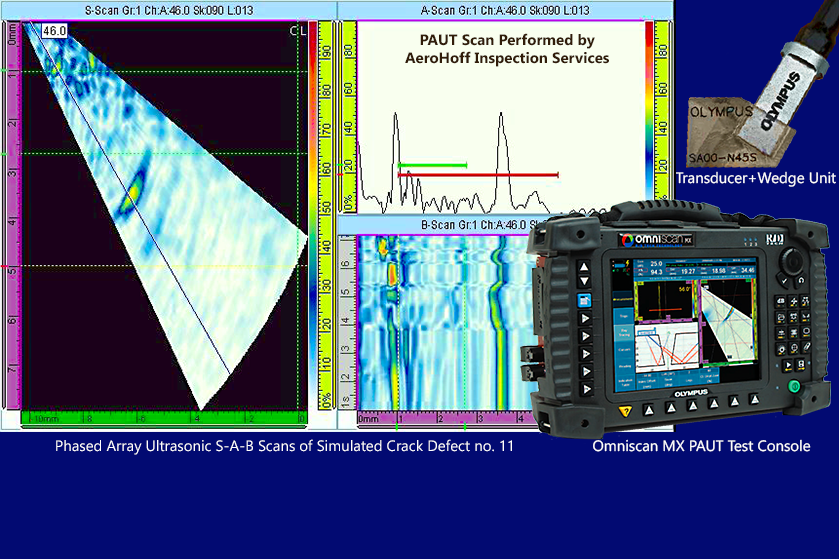
- baseline scanning using refracted shear waves
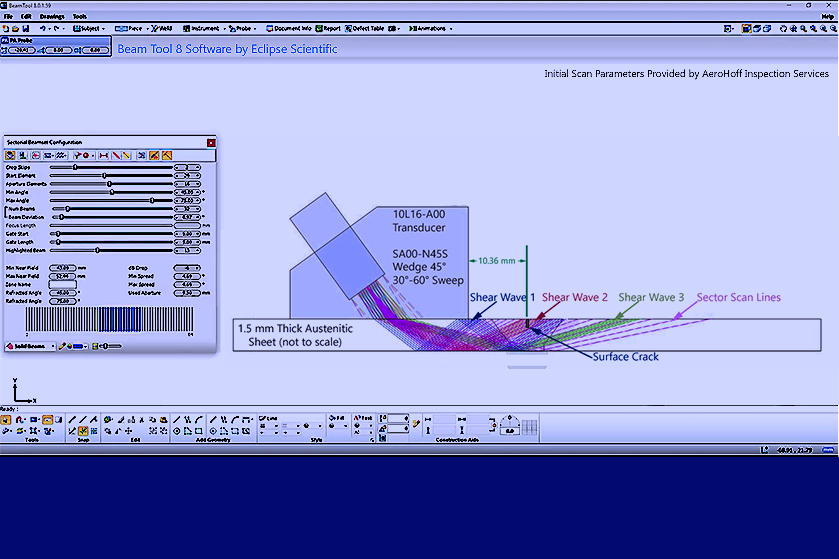
- software scan planning followed by probability of detection validation



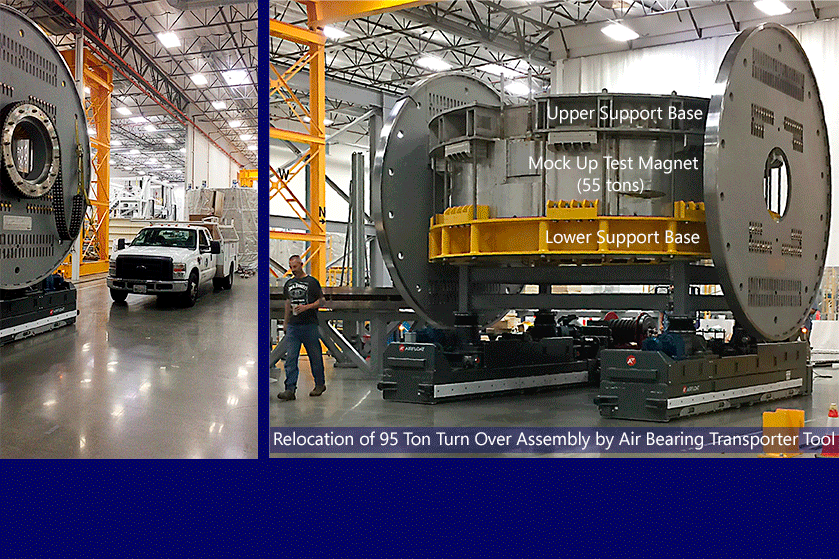
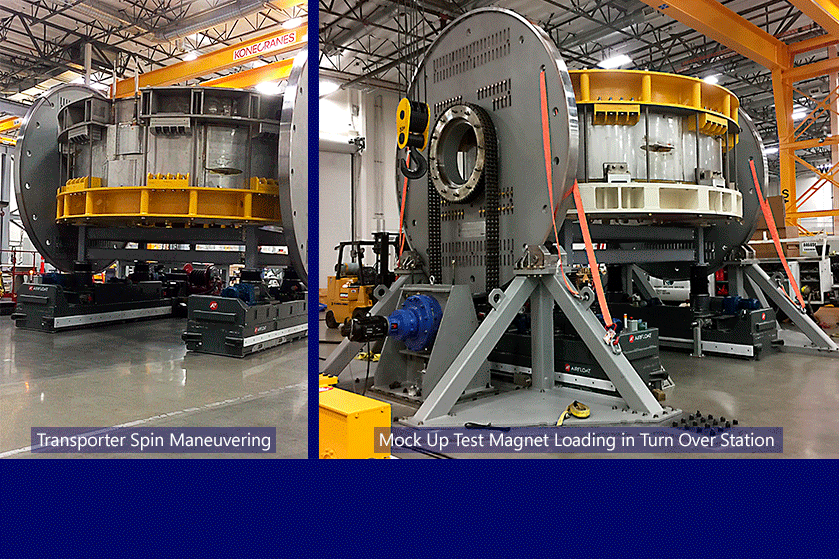



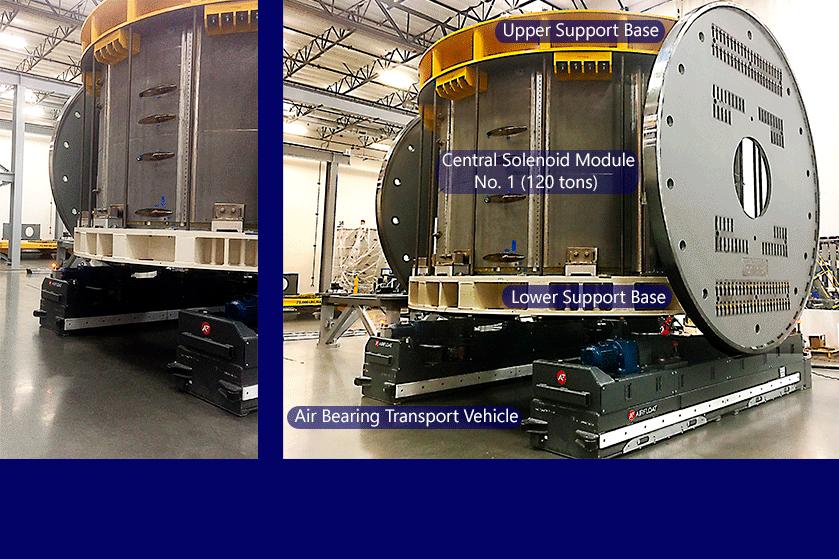
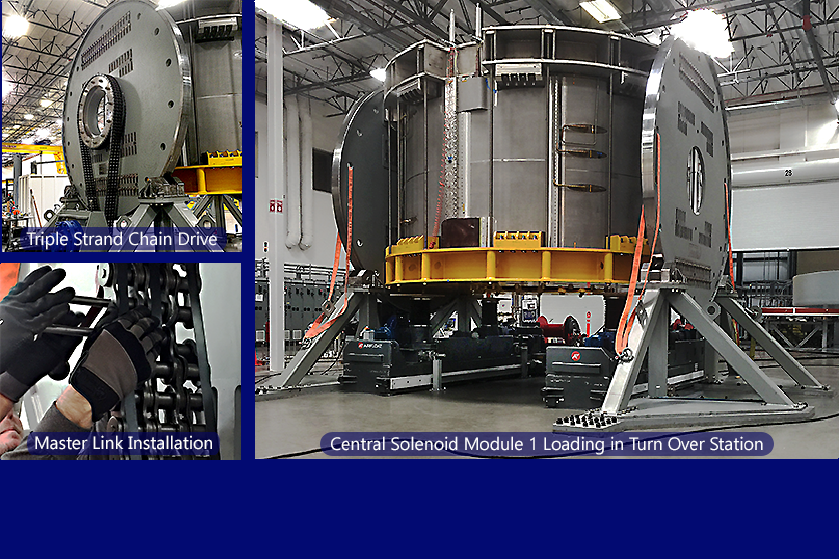
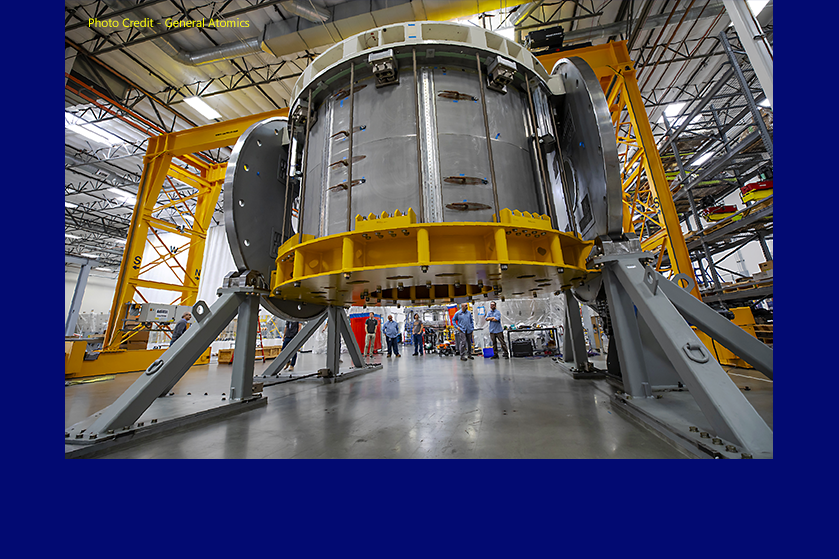
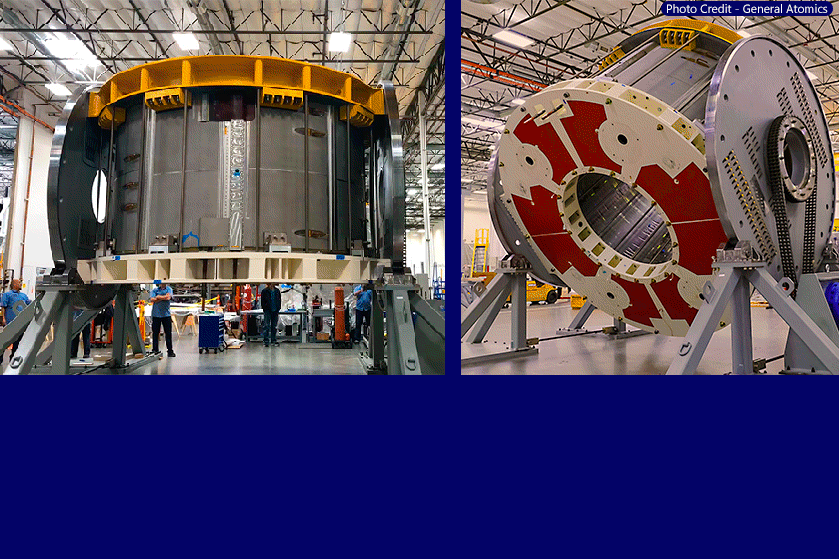
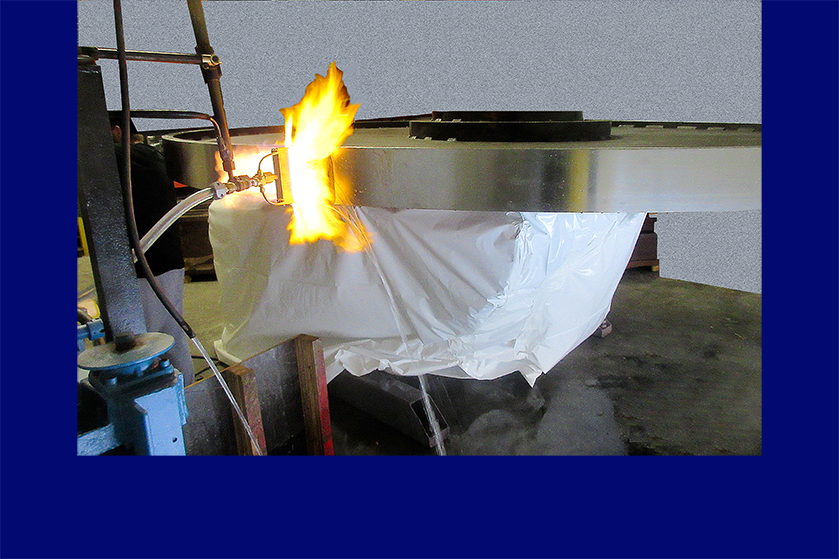

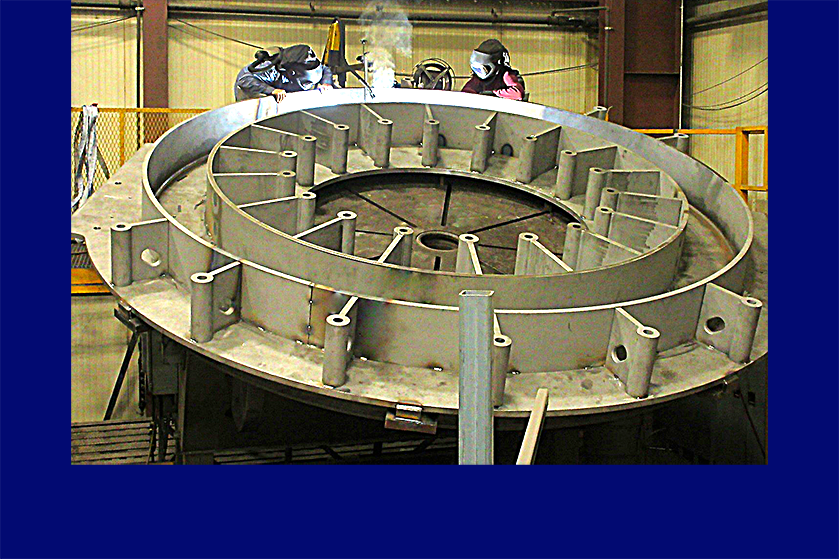


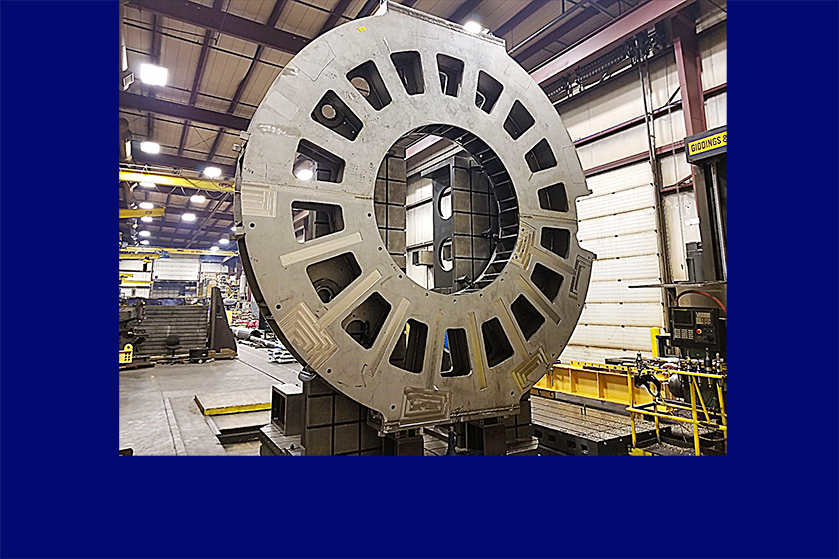
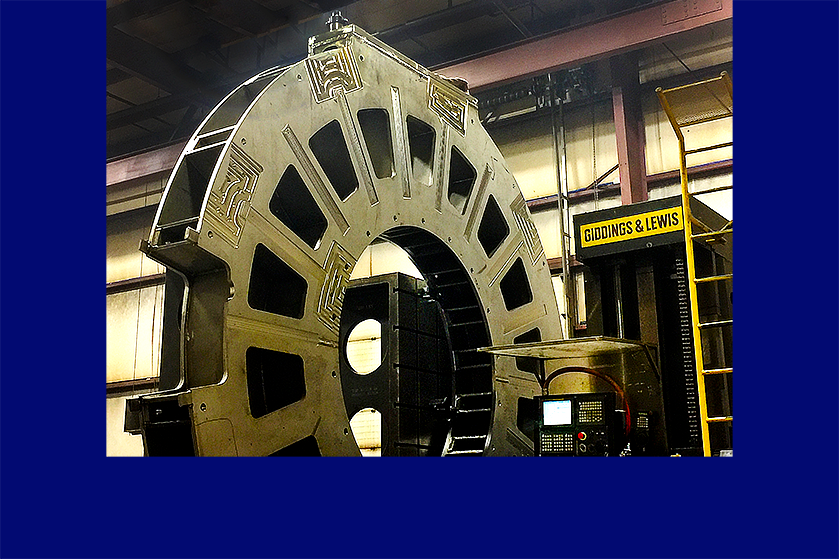



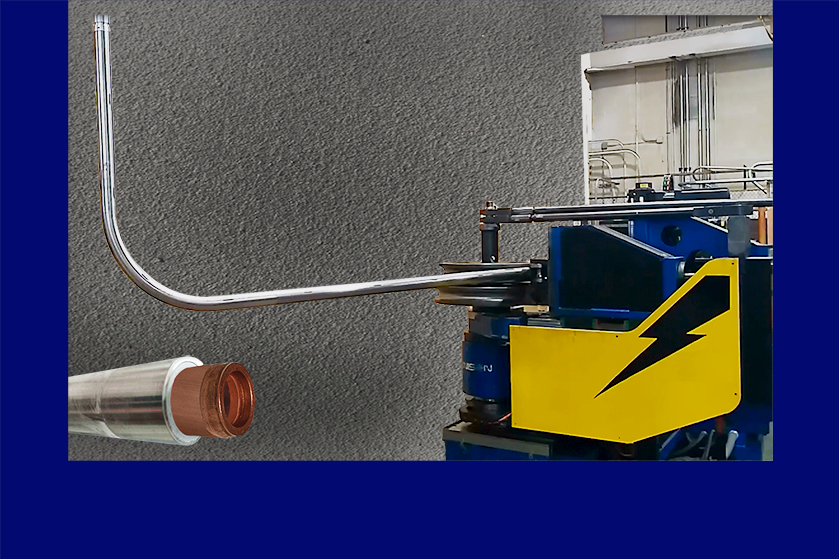


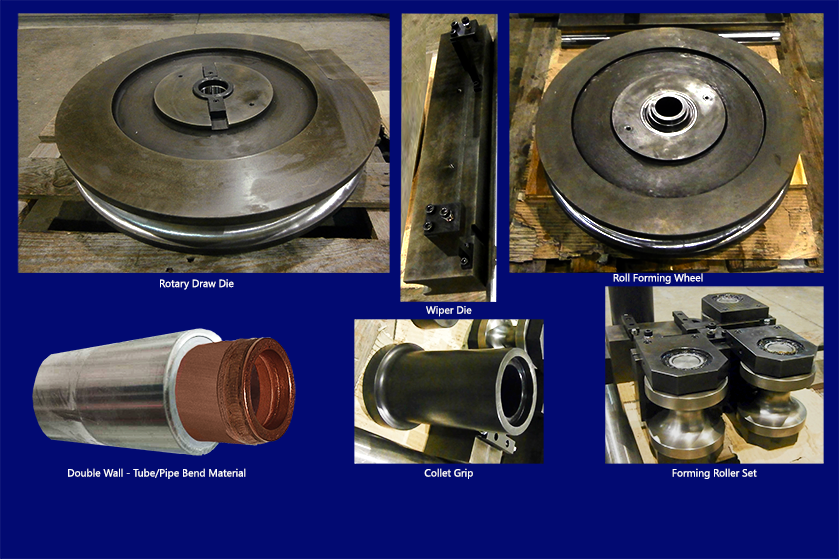
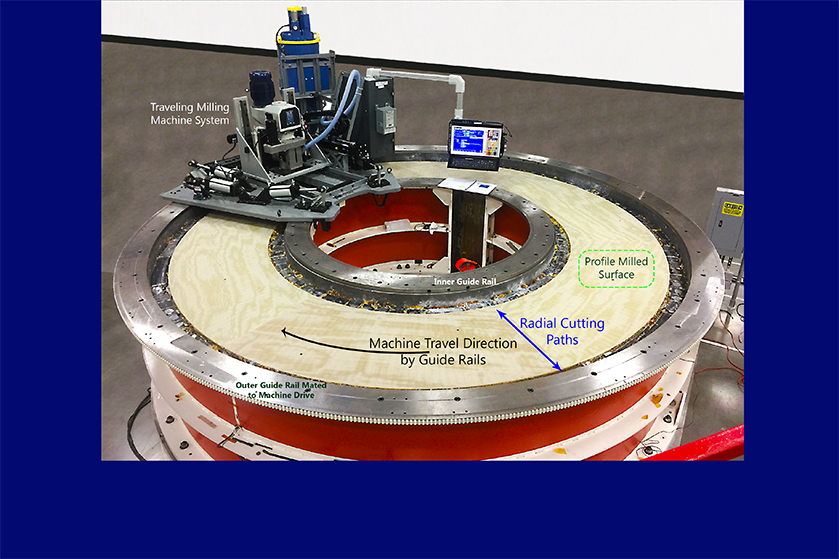
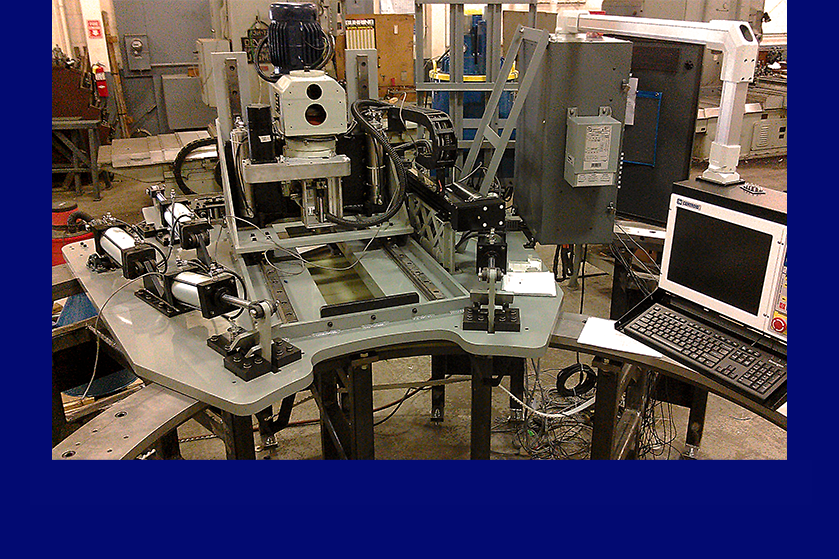
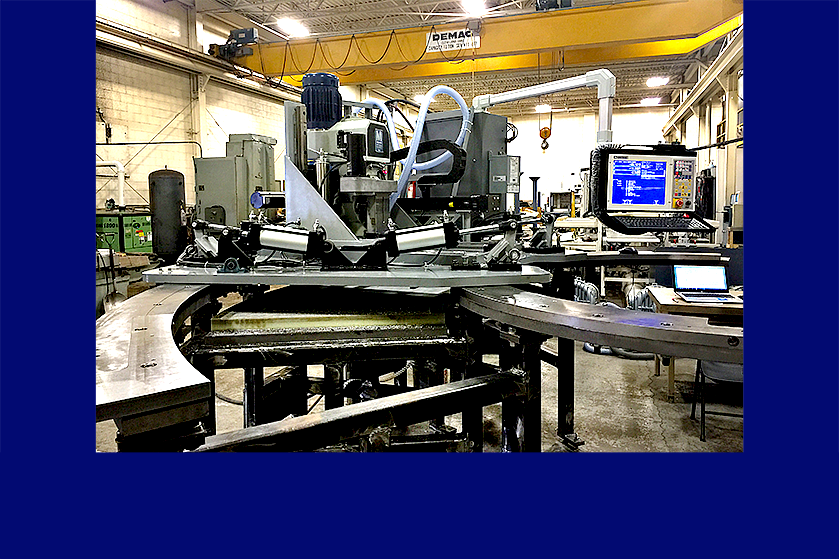
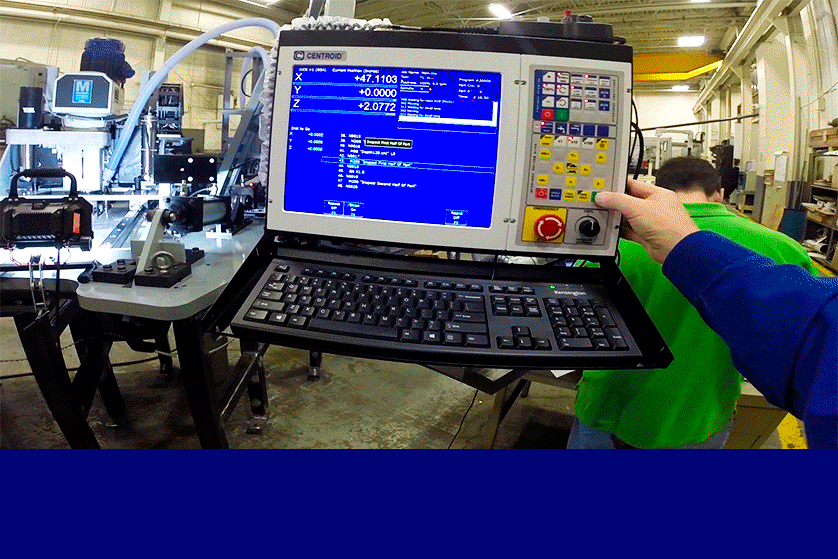
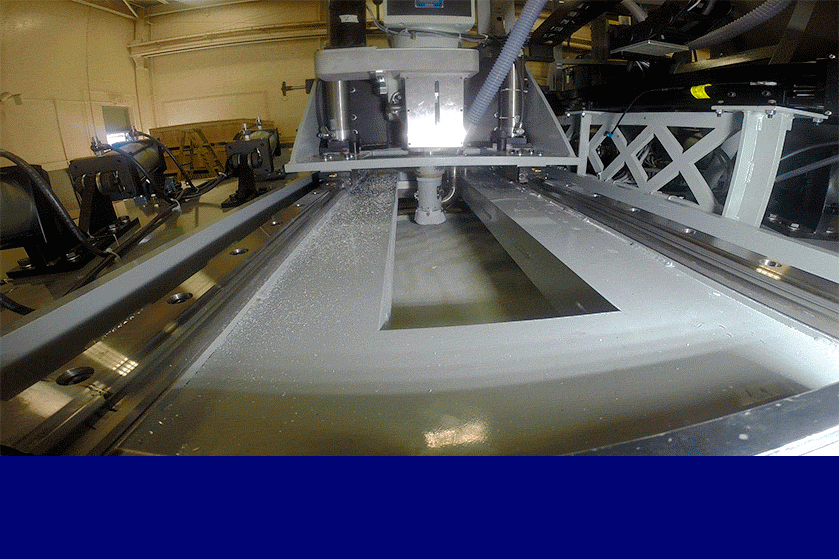
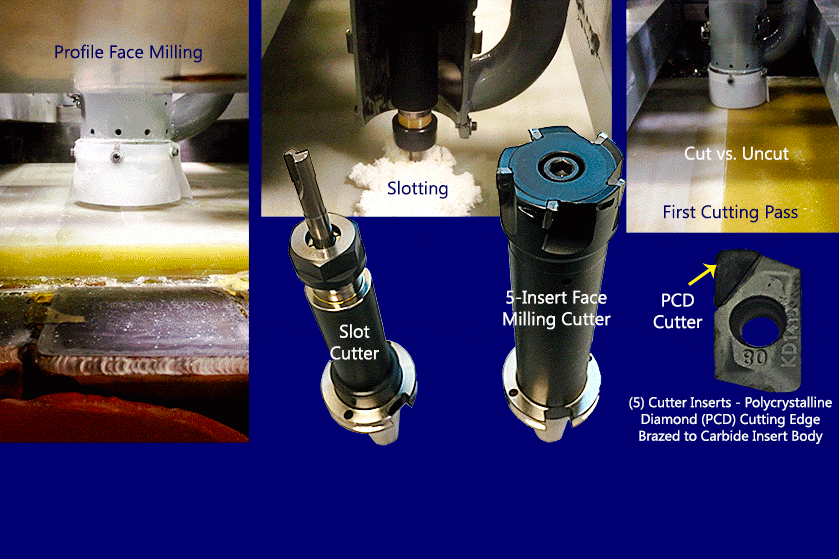
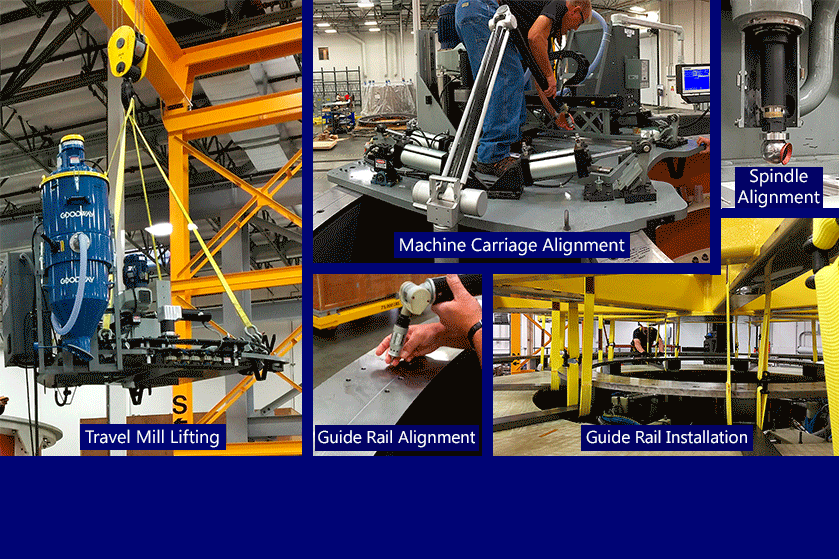
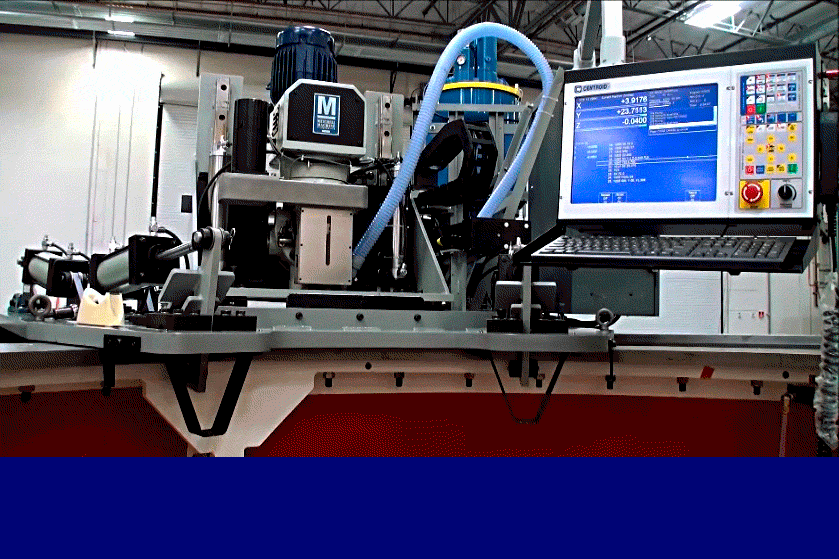
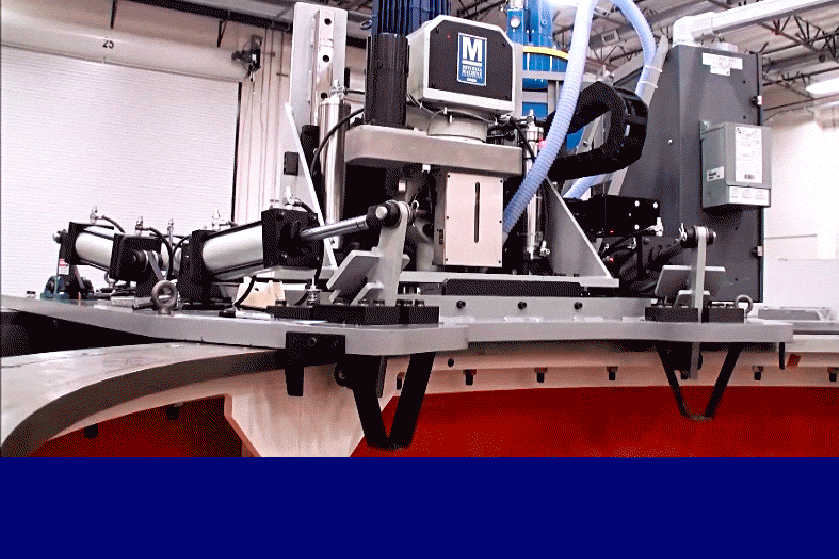


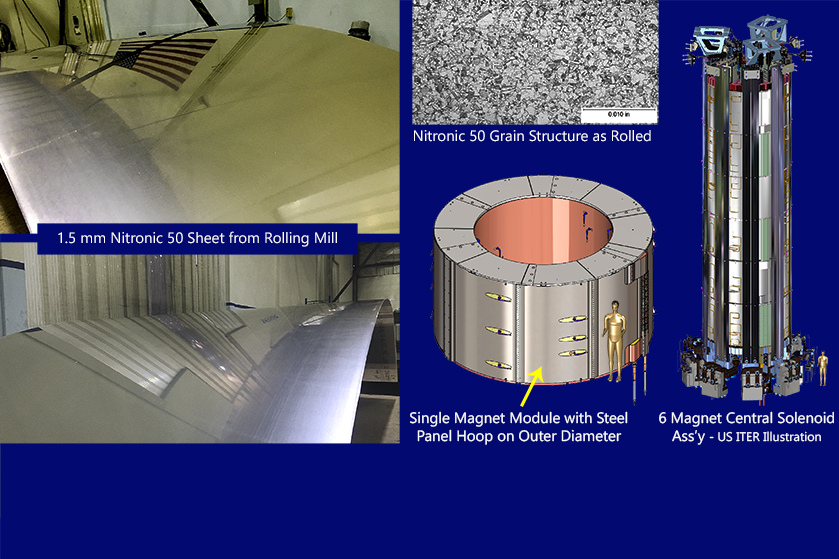
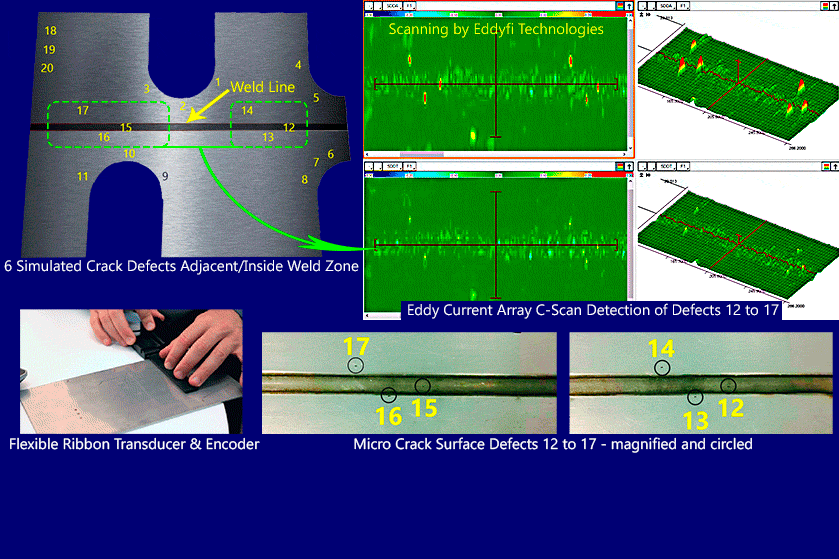
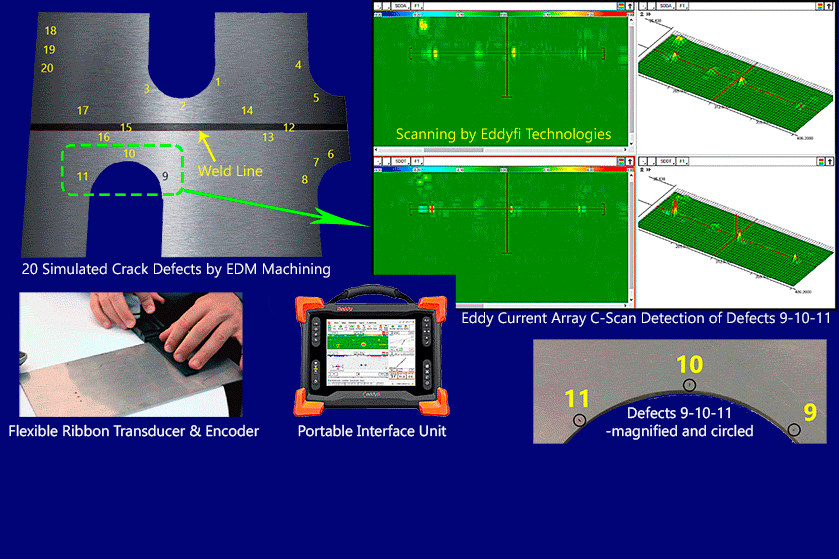
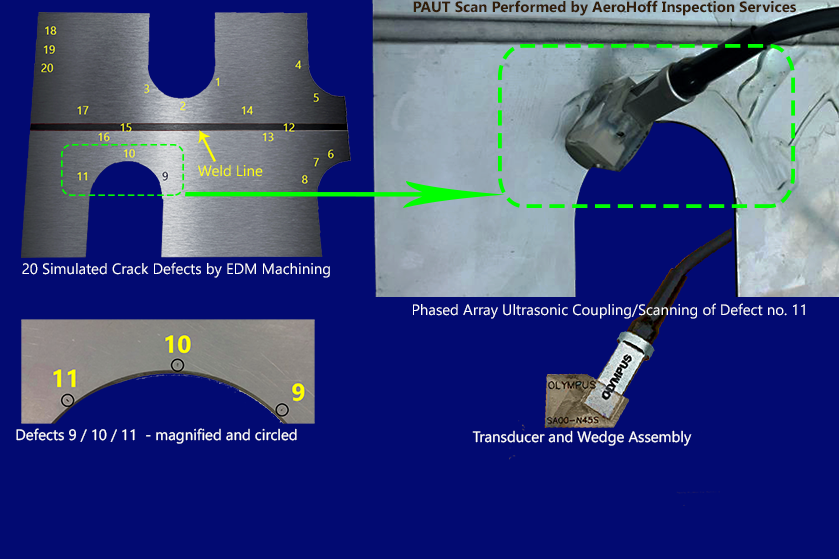
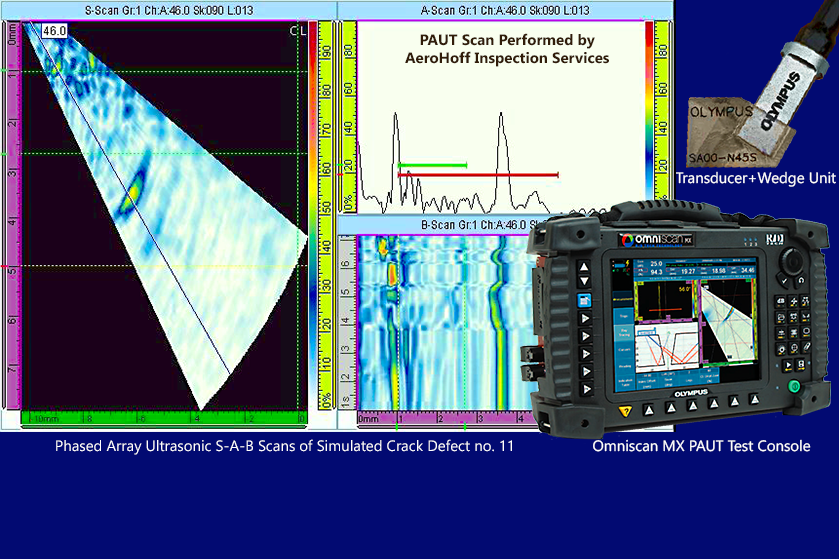
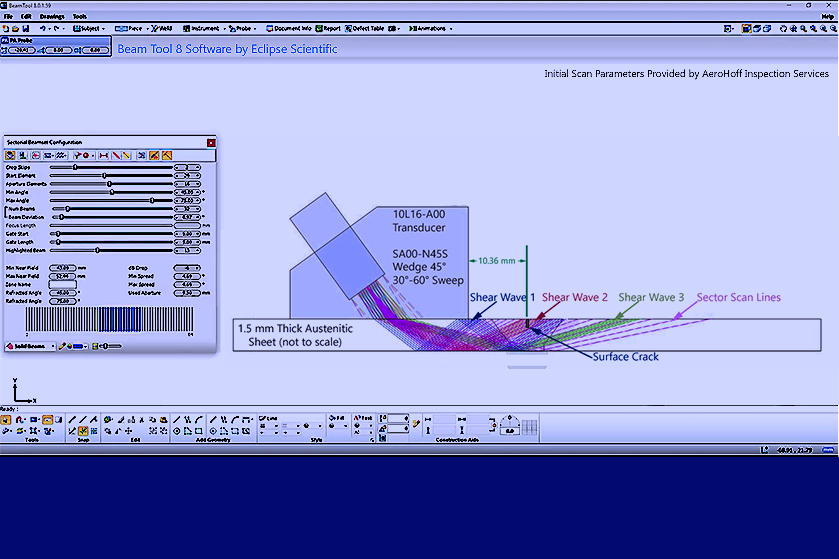